Introduzione
I microfusioni sono oggi uno dei metodi di produzione più popolari per le parti metalliche. Il processo di microfusione, definito anche processo a cera persa, è relativamente semplice, il che consente velocità di produzione rapide garantendo al contempo una precisione dimensionale costante. Le parti che sono tipicamente realizzate mediante microfusione includono quelle con geometria complessa come pale di turbine o componenti di armi da fuoco. Sono comuni anche applicazioni ad alta temperatura, che includono parti per l'industria petrolifera e del gas, automobilistica, aeronautica e militare. Le forcelle di trasmissione vengono ora prodotte utilizzando microfusione anziché forgiatura e lavorazioni complesse. Offre riduzione del peso, minore lavorazione, tempi di consegna migliorati e minori costi di trasporto delle scorte.
Le dimensioni del mercato globale del casting degli investimenti sono state stimate in 14.35 miliardi di dollari in 2018 e si prevede che crescano a un CAGR di 4.6% fino a 2025 secondo un rapporto di ricerche di mercato di Grand View Research. Esistono numerose applicazioni in cui le fusioni di investimento sono utilizzate principalmente: aerospaziale, produzione di energia, armi da fuoco, automobilistico, militare, commerciale, ristorazione, petrolio e gas, e le industrie energetiche utilizzano maggiormente questi componenti. L'aumento della penetrazione dei getti di investimento nella produzione di componenti avanzati come compressore, parti del motore, componenti del cambio e altri probabilmente aumenterà ulteriormente la domanda del mercato.
Nonostante le enormi aree di applicazione e la moderata domanda da parte dei settori dell'uso finale, questo settore si trova ad affrontare sfide legate all'efficienza, ai tempi di consegna e all'utilizzo della capacità. I leader del settore si stanno muovendo verso l'adozione di tecnologie più avanzate come l'automazione, l'internet delle cose industriale (IIoT) e le tecniche di simulazione. L'automazione nei processi di casting degli investimenti sta aiutando i produttori a ridurre i tempi di consegna, migliorare l'utilizzo della capacità e ottimizzare l'efficienza.
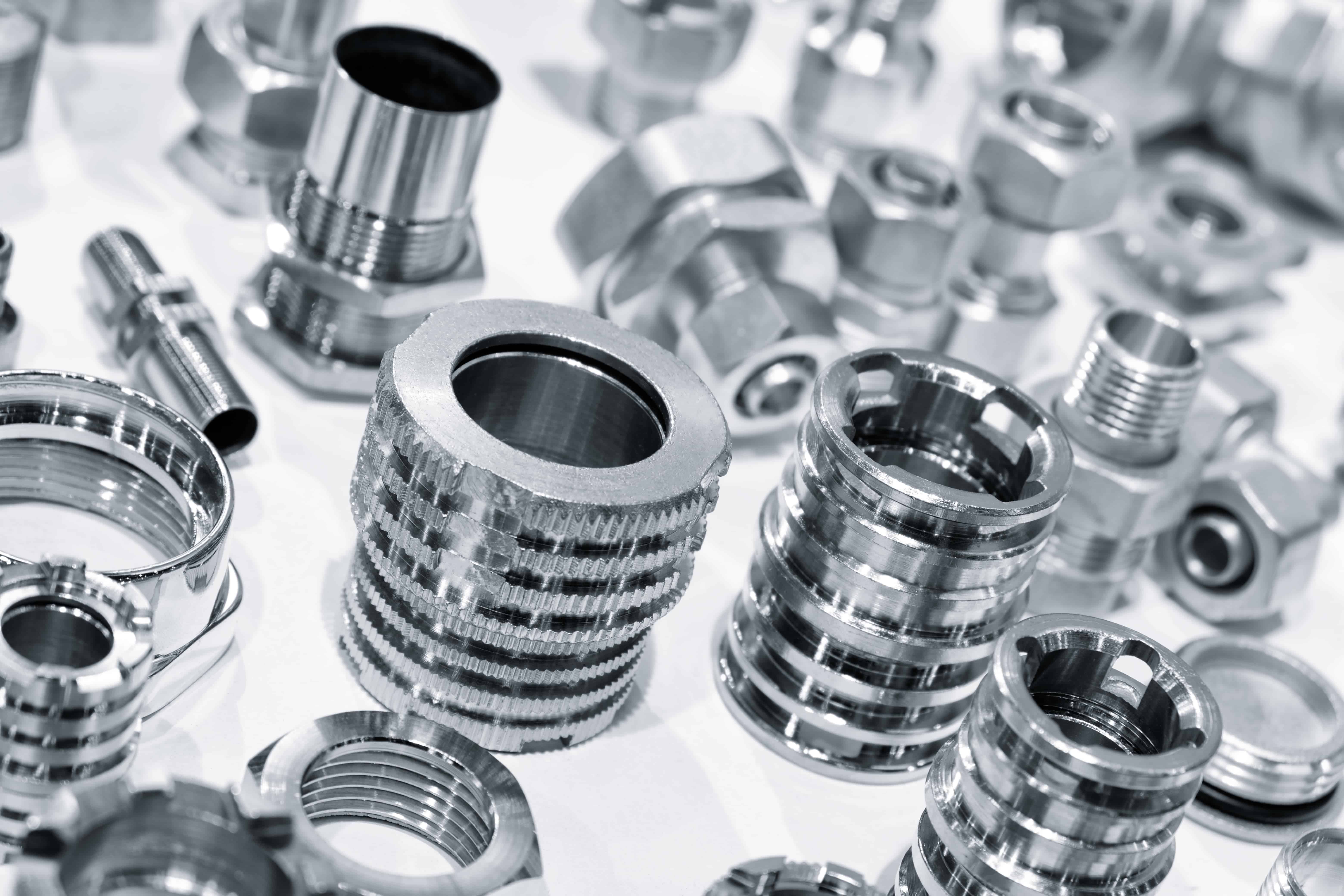
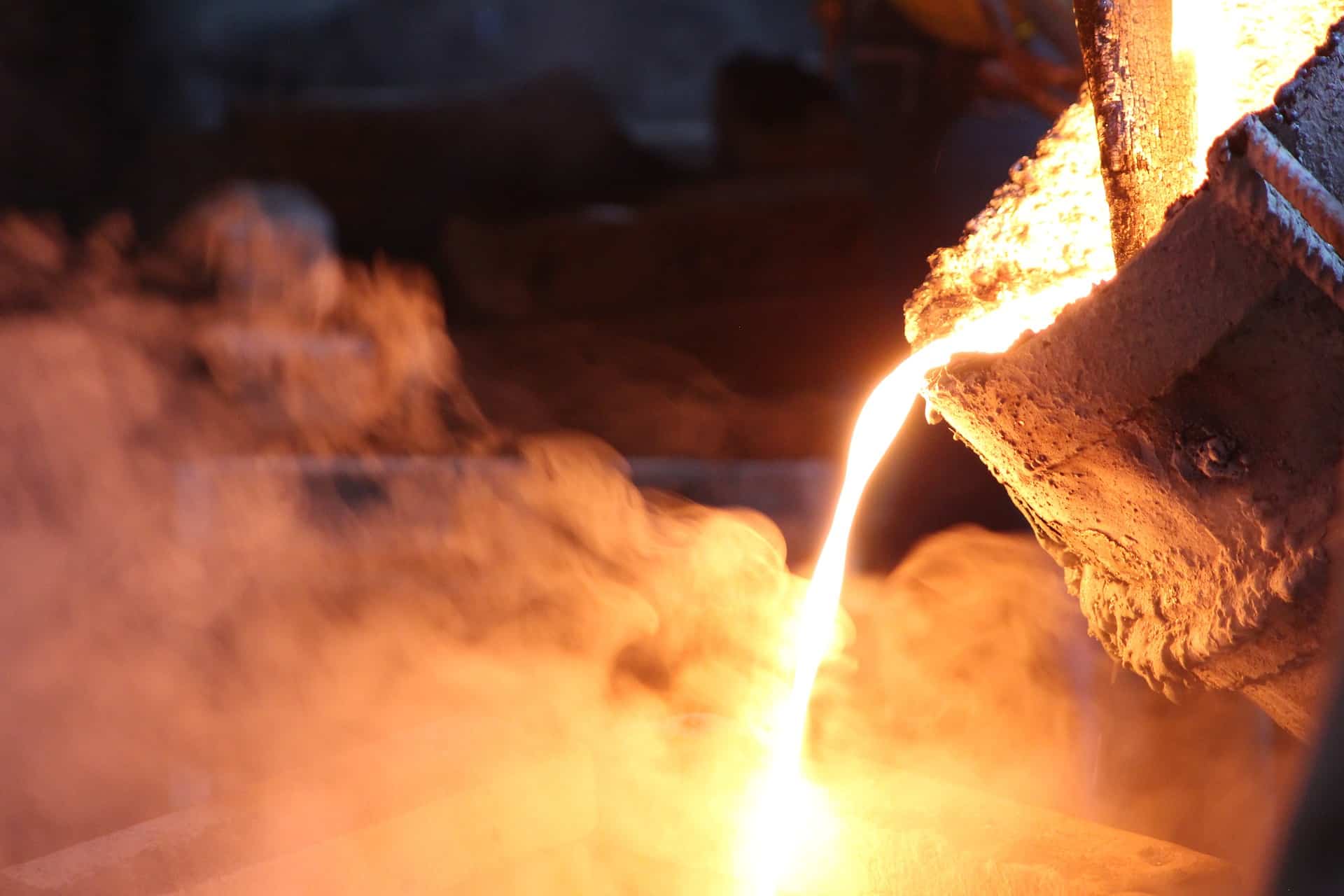
Applicazioni
La microfusione è un processo di fabbricazione in cui un modello di cera è rivestito con un materiale ceramico refrattario. Una volta indurito il materiale ceramico, la sua geometria interna assume la forma della fusione. La cera viene sciolta e il metallo fuso viene versato nella cavità dove si trovava il modello di cera. Il metallo si solidifica all'interno dello stampo ceramico e quindi il rivestimento metallico viene rotto.
Il rivestimento di materiale ceramico refrattario (liquame ceramico) può essere eseguito in stadi singoli o multipli, quest'ultimo spesso include un primo stadio incapsulante con controllo ad alta precisione dello spessore e della densità del rivestimento. Le parti del substrato possono essere permanenti o rimovibili dopo il rivestimento e la solidificazione per lasciare il rivestimento come parte autoportante (microfusione). Geometrie complesse della superficie del substrato e superfici rientranti interne possono essere rivestite in modo controllabile. La fusione in ceramica presenta particolari sfide per il raggiungimento di caratteristiche di liquame affidabili e per la loro misurazione affidabile, compresa la misurazione della viscosità per se stessa e come indicatore di altre caratteristiche. Dopo il rivestimento, le parti in ceramica vengono cotte per ottenere la massima resistenza, dimensioni e morfologia come prodotti finiti. Le rese dei prodotti utilizzabili dipendono da un rivestimento affidabile.
La qualità del guscio ceramico dipende dalla composizione del liquame e dal processo con cui è costruito. Gli ingredienti tipici di un impasto liquido da colata includono: silice colloidale, acqua e / o polimeri, agenti bagnanti, agenti antischiuma e farine refrattarie. Tutti questi ingredienti svolgono un ruolo importante nel comportamento del liquame e nelle proprietà risultanti del guscio. Le materie prime (refrattario, legante, agente bagnante e antischiuma) utilizzate per fare in modo che il liquame svolga un ruolo importante nel determinare le caratteristiche generali del guscio ceramico finale. La scelta adeguata dei materiali ceramici può portare a una finitura superficiale liscia e un'elevata precisione dei getti di metallo.
Viscosità liquida
Una buona composizione del liquame da sola non può garantire la produzione di gusci liberi lisci e difettosi se il liquame viene preparato in modo inadeguato. Le metodologie di controllo dei liquami variano considerevolmente tra le fonderie, a seconda delle linee di prodotti associate e delle specifiche richieste. L'obiettivo della preparazione dei liquami è produrre liquami stabili che devono soddisfare un determinato insieme di parametri dei liquami. Per essere considerati stabili, i fanghi devono essere accuratamente miscelati e i loro valori di viscosità devono essere stabili.
Il controllo dei liquami è una delle operazioni più importanti del processo di colata di investimento, con la viscosità del liquame come parametro critico. La viscosità del liquame è una misura delle caratteristiche di flusso del liquame ed è uno dei test di controllo più utilizzati nell'industria. I punti chiave su come la viscosità dei liquami è fondamentale nel processo di fusione degli investimenti sono i seguenti:
- La viscosità del liquame dipende dalla composizione (rapporto riempitivo / legante) e dal tempo di invecchiamento ed è un indicatore importante del stabilità dei liquami. Inizialmente è alto quando si mescolano i fanghi; tuttavia, mentre la miscelazione continua e il materiale refrattario viene bagnato e l'aria viene rilasciata, la viscosità diminuisce e si avvicina asintoticamente a un valore stabile.
- Finitura superficiale sarà una caratteristica importante della fusione, pertanto la qualità superficiale del guscio ceramico per la fusione a cera persa delle leghe metalliche deve essere adeguata. La finitura superficiale dipende fortemente dalla viscosità del liquame primario e dalla stabilità complessiva della miscela del liquame.
- La viscosità è un indicatore efficace del distribuzione delle dimensioni delle particelle della sospensione. I cambiamenti nella distribuzione delle dimensioni delle particelle di farina di ceramica (polvere) possono influire sulle proprietà del liquame, tra cui densità del liquame, reologia e spessore del rivestimento. Le proprietà della shell che possono essere interessate sono permeabilità, caratteristiche termiche, spessore, copertura dei bordi e resistenza. Per applicazioni critiche come il titanio e la fusione DS/SC, il controllo delle dimensioni delle particelle può fare la differenza tra successo e fallimento. Monitoraggio continuo della viscositàoring e apportare le modifiche necessarie all'impasto liquido è essenziale per ottenere le giuste proprietà del guscio ceramico ed eventualmente dei getti di investimento.
- Il controllo continuo del processo è essenziale per raggiungere l'obiettivo resistenza alla flessione del guscio di investimento. L'aumento della viscosità del liquame aumenta la resistenza alla flessione dell'involucro dell'investimento, ma diminuisce oltre una viscosità limitante. Può essere attribuito a un maggiore contenuto di farina refrattaria per un dato contenuto di legante.
- La selezione di qualsiasi materiale di riempimento refrattario per la produzione del guscio dipende da un'ampia varietà di fattori che possono influenzare le proprietà dell'impasto liquido di rivestimento, del guscio e della colata, nonché l'economia del processo. In generale, la farina di zirconio viene utilizzata come materiale primario per l'impasto liquido nel processo di fusione a cera persa con guscio ceramico, ma è molto costosa. Pertanto, monit continuooring e il controllo della viscosità possono mantenere bassi i costi dei processi con un notevole risparmio di materiale, un ridotto utilizzo di solventi e un utilizzo ottimale dell'energia durante il processo di miscelazione.
- È necessario mantenere una viscosità dei liquami appropriata evitare problemi di shell come il cracking. Lo strato primario deve resistere alla pressione esercitata dall'espansione della cera poiché viene riscaldato durante la fase di rimozione della cera, oltre a sopravvivere ai rigori della manipolazione durante il processo di costruzione della conchiglia
Viscosità liquida è un parametro di progettazione importante ed è molto importante assicurarsi che rimanga entro l'intervallo predeterminato durante la fase di rivestimento per fornire uno spessore di rivestimento uniforme e proprietà del guscio desiderabili. Quando la viscosità fluttua al di fuori delle specifiche, il rivestimento del liquame ceramico sarà irregolare, il che alla fine porterà a una scarsa qualità e influisce sulle proprietà del guscio di investimento. Le proprietà del guscio che possono essere influenzate dalla viscosità del liquame sono rugosità superficiale, conducibilità termica, reattività chimica, permeabilità e resistenza del guscio. Le soluzioni di rivestimento altamente viscose provocano appiccicosità e causano difficoltà di trasferimento sul substrato, mentre la bassa viscosità rende più mobile e più difficile il controllo e comporta anche un maggiore utilizzo di solvente. La viscosità aumenta quando non viene lavorata e diminuisce quando vi è una forza applicata costante. La forte correlazione tra temperatura e viscosità del liquame suggerisce che le fluttuazioni della temperatura possono avere un impatto drastico sulla viscosità, e quindi il processo di rivestimento in generale.
Al fine di avere un rivestimento uniforme e di non sprecare materiali e ottimizzare l'utilizzo di energia, è quindi altamente desiderabile che la viscosità del liquame sia regolata automaticamente su un valore sostanzialmente costante. Monitoraggio della viscosità in linea in tempo realeoring e controllo nel processo di rivestimento è essenziale migliorare le prestazioni e ridurre i costi in quasi tutti i processi di rivestimento di microfusione. Gli operatori di processo comprendono la necessità di un viscosimetro che monitora la viscosità e la temperatura e potrebbe utilizzare la viscosità con compensazione della temperatura come variabile di processo chiave per garantire coerenza e ridurre i tassi di scarto dei getti di investimento finali.
pH della sospensione e suo effetto sul rischio di gelificazione
Nel processo di rivestimento, la sospensione viene mantenuta nel processo a una viscosità costante con la reazione del gel che si verifica. Ciò si ottiene aggiungendo acqua in eccesso in modo tale da ridurre il contenuto di silice. In effetti, la diluizione significa che le particelle di silice sono più distanti, e quindi interagiscono meno frequentemente, e viene mantenuto un certo grado di stabilità. Tuttavia, un contenuto sempre decrescente di silice e l'aumento della viscosità del legante non sono mai una buona cosa e alla fine il liquame perde il suo potere legante perché la silice è così ridotta, oppure la scarsa caratteristica di flusso porta a una scarsa costruzione del guscio con conseguenti difetti di fusione.
Abbassare il pH riduce le forze repulsive che mantengono separate le particelle colloidali e possono far collidere e gelare le particelle, pertanto il pH dei fanghi è fondamentale e un fattore chiave per la qualità del liquame. In generale, quando il pH di una sospensione si avvicina ai limiti minimi o massimi raccomandati, la sospensione è a un valore maggiore rischio di gelificazione. I materiali refrattari, le cere e l'acqua possono tutti contenere componenti che riducono il pH dei liquami. La crescita dei microbi riduce anche il pH dei liquami. I microbi possono essere controllati con l’aggiunta di biocidi, mentre la scelta delle cere e dei materiali refrattari potrebbe non essere facilmente controllata. Il pH dei liquami può essere aumentato mediante l'aggiunta di idrossido di ammonio diluito e trietanolammina. Pertanto, monit continuooring e il controllo del valore del pH attraverso il controllo del feedback del liquame può ridurre il rischio di gelificazione.
Perché la viscosità (e il pH) monitoring e il controllo sono fondamentali nel processo di rivestimento con impasto liquido della microfusione?
I vantaggi ampi e significativi con la gestione della viscosità e del pH nel processo di rivestimento in sospensione del getto di investimento sono:
- Shell di investimento e qualità della fusione: Gli investimenti iniziali devono essere conformi alle specifiche del prodotto finito e il controllo del processo è fondamentale per ottenere lo stesso risultato. La variazione della viscosità provoca un cambiamento significativo nella qualità del rivestimento. La finitura superficiale dipende fortemente dalla viscosità dell'impasto liquido primario e dalla stabilità complessiva della miscela di impasto liquido. Monitoraggio della viscosità in lineaoring e il controllo possono aiutare a ottenere la qualità del rivestimento richiesta.
- Ridurre i difetti: Il controllo della viscosità può aiutare ad alleviare la frequenza di miscele nel processo di rivestimento: incollaggio e raccolta, gemellaggio, peeling, scissione, screpolatura, rugosità, formazione di bolle, ponti ed erosione superficiale e ridurre le scarse caratteristiche di flusso che portano a una scarsa formazione del guscio con conseguenti difetti di colata.
- Resa migliore: Garantire la coerenza durante tutto il processo di rivestimento riduce significativamente i tassi di scarto, risparmiando costi e tempi e favorendo i processi di colata continua. Le tecniche di misurazione offline sono noiose e inaffidabili e comportano enormi ritardi nel processo di produzione oltre a sostenere costi elevati del personale per campionare ed eseguire i test.
- Proprietà corrette: Una scarsa qualità del rivestimento può influire negativamente sulle proprietà desiderabili dei gusci di investimento: rugosità superficiale, conducibilità termica, reattività chimica, permeabilità e resistenza del guscio a loro volta influenzano la qualità dei getti di investimento. Tutte queste proprietà dipendono dal grado di controllo del processo di rivestimento, pertanto è fondamentale controllare la viscosità.
- Processi efficienti: L'automazione della viscosità e il rilevamento del pH e il controllo nei processi di fusione degli investimenti possono aiutare i produttori a ridurre i tempi di consegna, migliorare l'utilizzo della capacità e ottimizzare l'efficienza.
- Costo: Il rivestimento con una viscosità errata danneggia più della semplice qualità. Una cattiva gestione della viscosità aumenta l'utilizzo di polvere, legante e solventi, incidendo sui margini di profitto. Le misurazioni continue della viscosità durante il processo di miscelazione possono garantire omogeneità, ottimizzare l'utilizzo di energia e ridurre l'uso di solvente.
- Rifiuto: I materiali rifiutati a causa della scarsa qualità possono essere ridotti con una corretta gestione della viscosità.
- Efficienza: L'eliminazione del controllo manuale della viscosità libera il tempo degli operatori e consente loro di concentrarsi su altre attività.
- Eco-compatibile: Ridurre l'uso di pigmenti e solventi fa bene all'ambiente.
- Conformità normativa: Le normative globali e nazionali guidano le proprietà complessive dei getti di investimento. La mancata adesione a causa della variabilità della produzione potrebbe comportare danni significativi e perdita dei clienti oltre alle responsabilità derivanti da difetti di fabbricazione nel processo di produzione.
Per garantire un rivestimento uniforme e di alta qualità, la variazione di viscosità durante tutto il flusso del processo viene monitorata in tempo reale, effettuando misurazioni da una linea di base anziché semplicemente misurando valori assoluti e apportando regolazioni della viscosità regolando i solventi e compensando la temperatura per mantenere l'intero processo di rivestimento entro i limiti specificati. Con monitoraggio continuo della viscosità onlineoring, la formazione iniziale del guscio può essere controllata in modo più efficace, migliorando quindi significativamente le proprietà metallurgiche del prodotto finale.
Sfide di processo
Gli operatori nel mercato delle fusioni riconoscono la necessità di monitorare la viscosità, ma nel corso degli anni tale misurazione al di fuori del laboratorio ha sfidato ingegneri di processo e dipartimenti di qualità. I viscosimetri di laboratorio esistenti hanno scarso valore negli ambienti di processo perché la viscosità è direttamente influenzata dalla temperatura, dalla velocità di taglio e da altre variabili che sono molto diverse da quelle in linea. I metodi convenzionali per il controllo della viscosità del rivestimento in sospensione si sono dimostrati inadeguati anche in applicazioni in cui è consentita un'ampia variazione di viscosità.
Tradizionalmente, gli operatori del settore della microfusione hanno misurato la viscosità del liquame utilizzando la coppa di flusso Zahn. La misurazione viene riportata come tempo trascorso affinché il volume della tazza scorra attraverso un foro nella parte inferiore della tazza. Il punto finale del test deve essere scelto in modo che sia coerente da test a test. La procedura è complicata e richiede tempo. È inaccurato, incoerente e non ripetibile anche con un operatore esperto. Nel processo di colata continua, l'intervallo di campionamento provoca ritardi eccessivi. La viscosità del liquame non può essere regolata in tempo reale. Inoltre, i vari contenitori contenenti il liquame sono aperti; a causa delle variazioni della temperatura ambiente, dell'umidità e di altri fattori, quali temperatura, clima secco, è probabile che i solventi siano volatili, quindi la tecnica di misurazione della viscosità basata sulla tazza diventa inefficace.
La viscosità e le altre caratteristiche ad essa correlate (ad es. Velocità di taglio e percentuale in peso dei solidi) variano in base alla profondità in un serbatoio contenente quantità sostanziali di liquame ceramico, condizioni di movimento del liquame (generalmente indotte a mantenere l'omogeneità), acquisizione da parti di fusione e riempimento o regolazioni. Esistono diversi approcci per misurare la viscosità online attraverso le sonde dello strumento inserite nel bagno di colata a varie profondità, ma sono state soggette a deriva ed errore nel corso delle operazioni di colata e alcune potrebbero richiedere frequenti rimozioni, pulizia o sostituzione, tempi di fermo e ricalibrazione delle sonde e degli strumenti. Alcune sonde possono essere pulite in situ ma sono soggette a malfunzionamento a causa dell'esposizione a rivestimenti indesiderati e variabili degli elementi del trasduttore.
Rheonics' Soluzioni
La misurazione e il controllo automatizzati della viscosità in linea sono fondamentali per controllare la formulazione del rivestimento e la viscosità dell'applicazione. Rheonics offre le seguenti soluzioni, basate su un risonatore torsionale bilanciato, per il controllo e l'ottimizzazione del processo di rivestimento:
- Online Viscosità misure: Rheonics' SRV è un dispositivo di misurazione della viscosità in linea ad ampio raggio con misurazione della temperatura del fluido integrata ed è in grado di rilevare in tempo reale le variazioni di viscosità all'interno di qualsiasi flusso di processo.
- Online Viscosità e densità misure: Rheonics' SRD è uno strumento di misurazione simultanea in linea di densità e viscosità con misurazione della temperatura del fluido integrata. Se la misurazione della densità è importante per le tue operazioni, SRD è il sensore migliore per soddisfare le tue esigenze, con capacità operative simili all'SRV e misurazioni accurate della densità.
Il sensore è incapsulato ermeticamente e quindi le prestazioni non sono influenzate dalla turbolenza e dalla disomogeneità del fluido. La misurazione automatizzata della viscosità in linea tramite SRV o SRD elimina le variazioni nel prelievo dei campioni e nelle tecniche di laboratorio. Il sensore viene installato nel secchio del rivestimento o nella linea attraverso la quale il rivestimento viene pompato all'applicatore, misurando continuamente la viscosità del sistema formulato (e la densità in caso di SRD). La consistenza del rivestimento si ottiene attraverso l'automazione del sistema di dosaggio tramite un controller di processo basato su misurazioni di viscosità e temperatura in tempo reale. Utilizzando un SRV / SRD in una linea di processo di rivestimento, l'efficienza del trasferimento del rivestimento viene migliorata migliorando la produttività, i margini di profitto e gli obiettivi ambientali / normativi. I sensori hanno un fattore di forma compatto per una semplice installazione OEM e retrofit. Non richiedono manutenzione o riconfigurazioni. I sensori offrono risultati accurati e ripetibili, indipendentemente da come o dove siano montati, senza bisogno di camere speciali, guarnizioni in gomma o protezione meccanica. Non utilizzando materiali di consumo, SRV e SRD sono estremamente facili da utilizzare senza manutenzione.
Rheonics offre un monitoraggio autonomo integrato della viscosità e del pHoring e sistema di controllo. IL Rheonics Liquame Monitoring e il sistema di controllo utilizza viscosimetri in linea con sonde pH in linea per monitorare la viscosità e il pH del liquame in tempo reale. Le valvole del solvente e dell'additivo vengono azionate per aggiungere la dose corretta per garantire il controllo assoluto delle caratteristiche dell'impasto liquido durante tutto il processo di miscelazione e rivestimento.
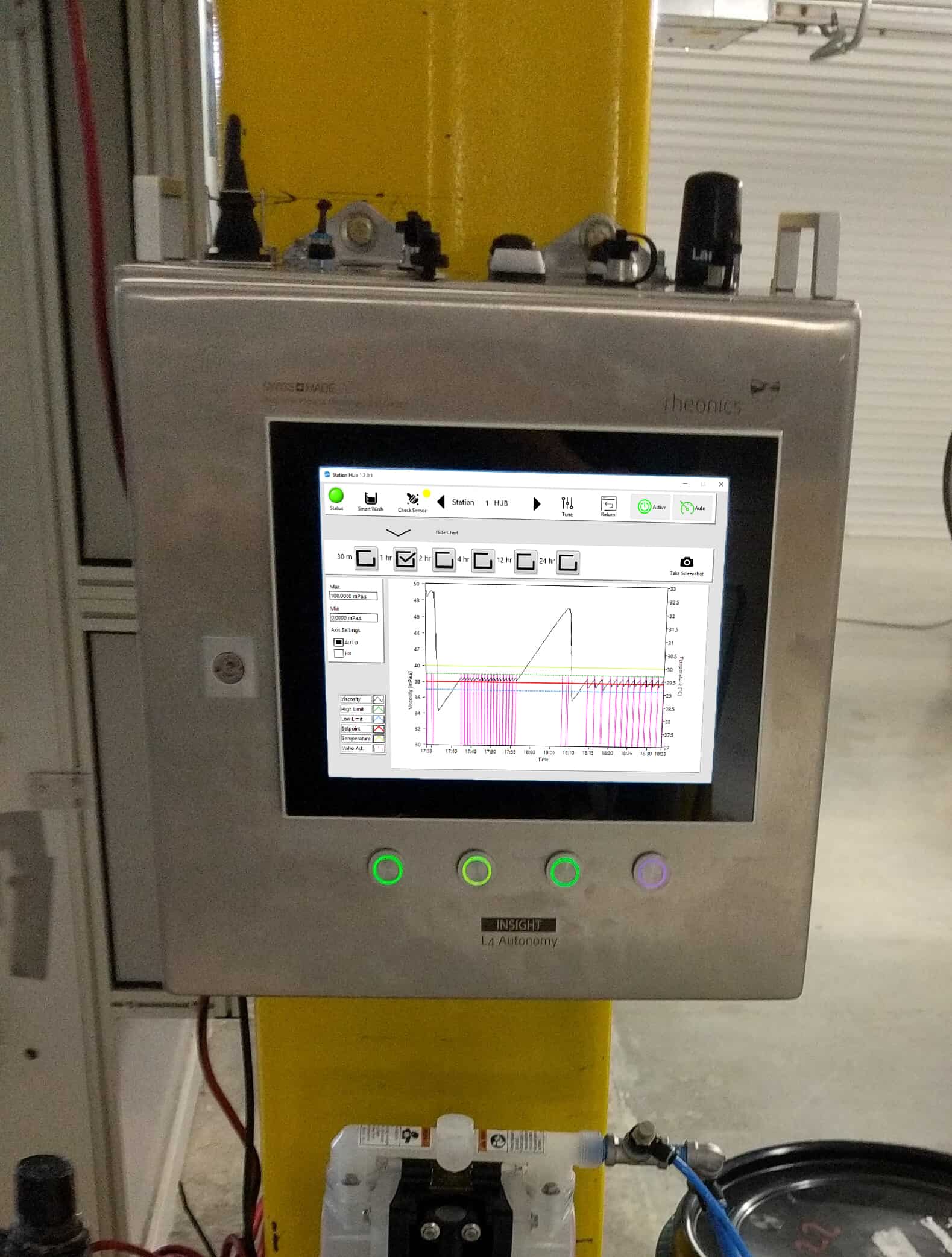
Rheonics'Vantaggio
Fattore di forma compatto, nessuna parte mobile e nessuna manutenzione
Rheonics' SRV e SRD hanno un fattore di forma molto piccolo per una semplice installazione OEM e retrofit. Consentono una facile integrazione in qualsiasi flusso di processo. Sono facili da pulire e non richiedono manutenzione o riconfigurazioni. Il loro ingombro ridotto consente una semplice installazione in linea, evitando qualsiasi spazio aggiuntivo o necessità di adattatori sulla verniciatrice.
Elevata stabilità e insensibilità alle condizioni di montaggio: qualsiasi configurazione possibile
Rheonics SRV e SRD utilizzano un esclusivo risonatore coassiale brevettato, in cui due estremità dei sensori ruotano in direzioni opposte, annullando le coppie di reazione sul loro montaggio e quindi rendendoli completamente insensibili alle condizioni di montaggio e alle portate. Questi sensori possono facilmente far fronte a spostamenti regolari. L'elemento sensore si trova direttamente nel fluido, senza la necessità di un alloggiamento speciale o di una gabbia protettiva.
Letture accurate istantanee delle condizioni - Panoramica completa del sistema e controllo predittivo
RheonicsIl software è potente, intuitivo e comodo da usare. La viscosità in tempo reale può essere monitorata su un computer. Più sensori sparsi in tutta la fabbrica vengono gestiti da un unico dashboard. Nessun effetto della pulsazione della pressione derivante dal pompaggio sul funzionamento del sensore o sulla precisione della misurazione. Inoltre, il sensore è insensibile ad eventuali vibrazioni o disturbi elettrici provenienti da macchinari esterni.
Installazione semplice e nessuna riconfigurazione / ricalibrazione necessaria
Sostituisci i sensori senza sostituire o riprogrammare i componenti elettronici con la modifica della struttura e i costi di implementazione più bassi.
Sostituzioni drop-in per sensore ed elettronica senza aggiornamenti del firmware o modifiche al coefficiente di calibrazione.
Facile montaggio. Si avvita in raccordi in linea filettati da ¾ ”NPT o connessioni flangiate.
Nessuna camera, O-ring guarnizioni o guarnizioni.
Facilmente rimosso per pulizia o ispezione.
SRV disponibile con flangia, DIN 11851 igienica e tri-clamp connessione per un facile montaggio e smontaggio.
Basso consumo energetico
Alimentatore CC 24V con assorbimento di corrente inferiore a 0.1 A durante il normale funzionamento (inferiore a 3W)
Tempi di risposta rapidi e viscosità compensata in temperatura
L'elettronica ultraveloce e robusta, combinata con modelli computazionali completi, rendono Rheonics dispositivi uno dei più veloci e precisi del settore. SRV e SRD forniscono misurazioni accurate della viscosità (e della densità per SRD) in tempo reale ogni secondo e non sono influenzati dalle variazioni della portata!
Ampie capacità operative
RheonicsGli strumenti sono costruiti per effettuare misurazioni nelle condizioni più difficili. SRV ha la più ampia gamma operativa sul mercato dei viscosimetri da processo in linea:
- Intervallo di pressione fino a 5000 psi e superiore
- Intervallo di temperatura da -40 fino a 300 ° C
- Intervallo di viscosità: 0.5 cP fino a 50,000 + cP
SRD: strumento singolo, tripla funzione - Viscosità, temperatura e densità
Rheonics' SRD è un prodotto unico che sostituisce tre diversi strumenti per misurazioni di viscosità, densità e temperatura. Elimina la difficoltà di co-localizzare tre diversi strumenti e fornisce misurazioni estremamente accurate e ripetibili nelle condizioni più difficili.
Ottieni la giusta qualità del mantello, riduci i costi e migliora la produttività
Integrare un SRV / SRD nella linea di processo e garantire uniformità e coerenza durante tutto il processo di rivestimento. Ottieni una qualità costante dei liquami senza preoccuparti delle variazioni di pH. SRV (e SRD) monitora e controlla costantemente la viscosità (e la densità in caso di SRD) e impedisce l'uso eccessivo di pigmenti e solventi costosi. Il controllo affidabile e automatico assicura che i processi vengano eseguiti più rapidamente e consente di risparmiare tempo agli operatori. Ottimizza il processo di rivestimento con un SRV e sperimenta minori tassi di scarto, minori sprechi, minori reclami dei clienti, minori arresti della stampa e risparmi sui materiali. E alla fine, contribuisce ad una migliore linea di fondo e ad un ambiente migliore!
Clean in place (CIP)
SRV (e SRD) monitora la pulizia delle linee di inchiostro tramite monitoring la viscosità (e densità) del solvente durante la fase di pulizia. Eventuali piccoli residui vengono rilevati dal sensore, consentendo all'operatore di decidere quando la linea è pulita allo scopo. In alternativa, SRV fornisce informazioni al sistema di pulizia automatizzato per garantire una pulizia completa e ripetibile tra un ciclo e l'altro. Le sonde del sensore non sono influenzate da alcuna esposizione e producono risultati ripetibili anche nelle condizioni più difficili.
Design e tecnologia dei sensori superiori
L'elettronica sofisticata e brevettata di terza generazione guida questi sensori e valuta la loro risposta. SRV e SRD sono disponibili con connessioni al processo standard del settore come ¾" NPT e 3" Tri-clamp consentendo agli operatori di sostituire un sensore di temperatura esistente nella linea di processo con un SRV/SRD che fornisce informazioni sui fluidi di processo estremamente preziose e utilizzabili come la viscosità oltre a una misurazione accurata della temperatura utilizzando un Pt1000 integrato (disponibile DIN EN 60751 Classe AA, A, B) .
Eco-compatibile
Ridurre l'uso di COV (composti organici volatili) nel processo riducendo l'energia necessaria per recuperarlo o i costi di smaltimento. Produce in modo intelligente risparmiando sui costi, garantendo alta qualità e proteggendo l'ambiente.
Elettronica costruita per soddisfare le tue esigenze
Disponibile sia in un alloggiamento del trasmettitore antideflagrante che in un montaggio su guida DIN con fattore di forma ridotto, l'elettronica del sensore consente una facile integrazione nelle tubazioni di processo e all'interno degli armadi delle macchine.
Facile da integrare
Molteplici metodi di comunicazione analogica e digitale implementati nell'elettronica del sensore rendono il collegamento a PLC industriali e sistemi di controllo semplici e diretti.
Conformità ATEX e IECEx
Rheonics offre sensori a sicurezza intrinseca certificati ATEX e IECEx per l'uso in ambienti pericolosi. Questi sensori sono conformi ai requisiti essenziali di salute e sicurezza relativi alla progettazione e costruzione di apparecchiature e sistemi di protezione destinati all'uso in atmosfere potenzialmente esplosive.
Le certificazioni di sicurezza intrinseca e antideflagrante possedute da Rheonics consente inoltre la personalizzazione di un sensore esistente, consentendo ai nostri clienti di evitare i tempi e i costi associati all'identificazione e al test di un'alternativa. Possono essere forniti sensori personalizzati per applicazioni che richiedono da una unità fino a migliaia di unità; con tempi di consegna di settimane anziché di mesi.
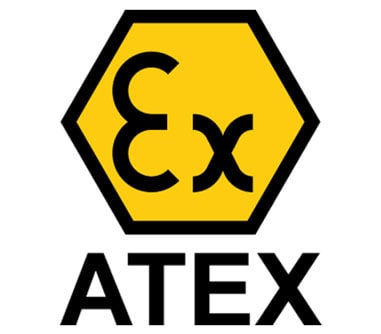
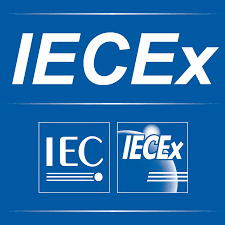
Implementazione
Installa direttamente il sensore nel flusso di processo per eseguire misurazioni di viscosità e densità in tempo reale. Non è necessaria alcuna linea di by-pass: il sensore può essere immerso in linea. La portata e le vibrazioni non influenzano la stabilità e l'accuratezza della misurazione. Ottimizza la miscelazione del liquame e le prestazioni del rivestimento durante la costruzione del guscio fornendo test ripetuti, consecutivi e coerenti sul fluido.
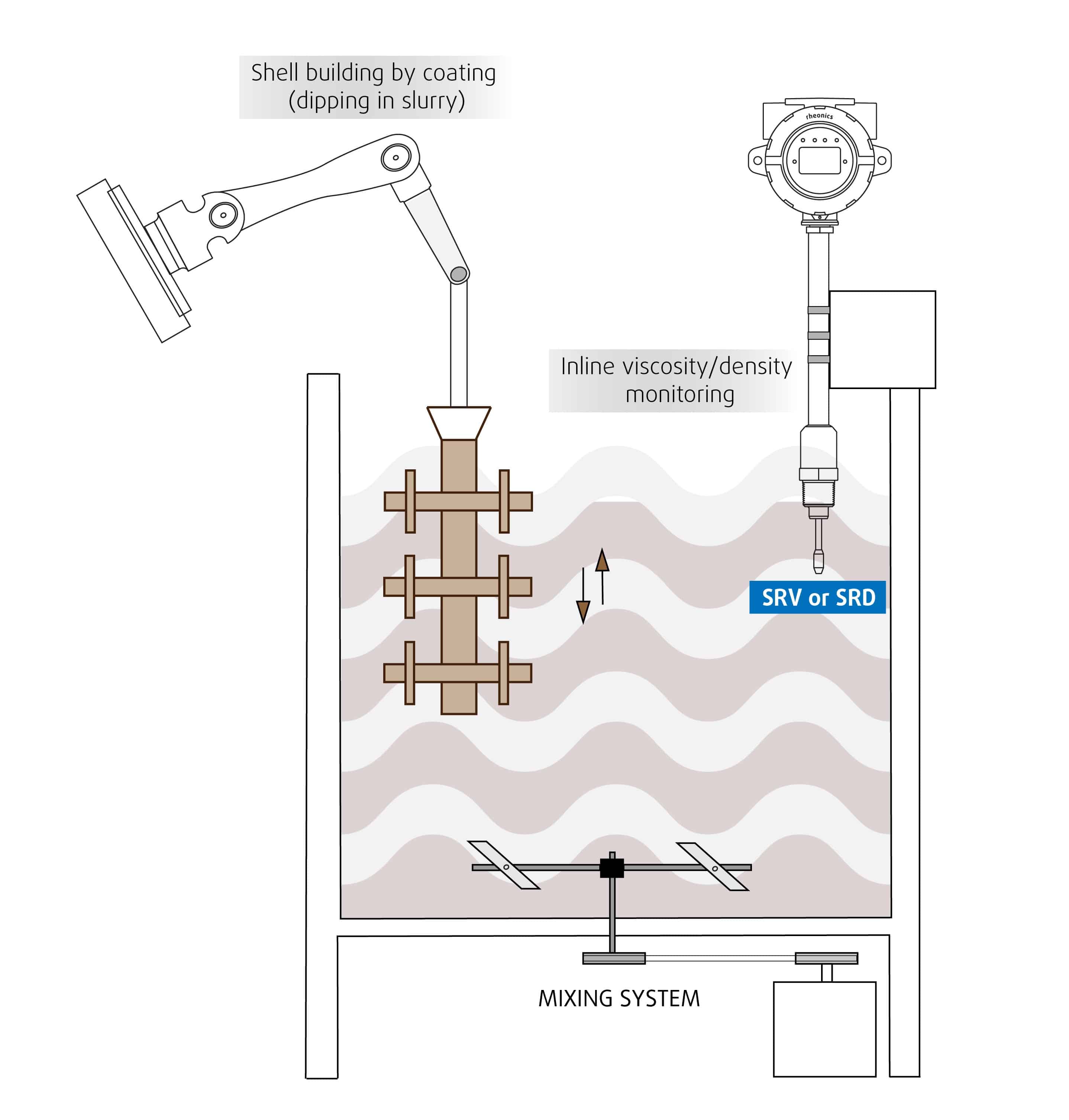
SRV / SRD in serbatoi di miscelazione di liquami ceramici durante la miscelazione e il rivestimento per la costruzione di shell - Schema con possibile posizione di montaggio del sensore
Aggiornamenti dell'applicazione - Da Rheonics Blog
Rheonics Sessione tecnica e stand al WCIC Expo, Investment Casting Institute – agosto 2022 ad Anaheim, California, USA
Argomento Controllo della viscosità per la costruzione di gusci di colata coerenti Data e ora 22 agosto 2022 @ 13:30 - 14:00, Anaheim, California,...
Rheonics Webinar tecnico – ICI (Investment Casting Institute) – Fonderia 4.0 – Costruzione di involucri efficaci, di alta qualità e senza difetti
Argomento Foundry 4.0 – La costruzione di involucri efficaci, di alta qualità, privi di difetti richiede il monitoraggio della viscosità in tempo realeoring e controllo dei fanghi ceramici Data…
Funzionalità INCAST Rheonics – “Fonderia 4.0 – La fusione intelligente di precisione necessita del controllo della viscosità dei fanghi ceramici”
Rivista focalizzata sul settore della fusione di investimenti - INCAST Mag (https://www.investmentcasting.org/current-issue.html) pubblica un articolo di approfondimento che copre Rheonics viscosimetro in linea SRV e...
Fonderie intelligenti: fattori che spingono i fonditori ad abbracciare l'industria 4.0 e la digitalizzazione
Molti parametri possono alterare la qualità dell'impasto ceramico nella colata a cera persa tra lotti: fluttuazioni di temperatura e umidità, apparecchiature di miscelazione...
Rheonics è ora membro dell'Investment Casting Institute
Siamo lieti di informarvi che ora siamo membri dell'Investment Casting Institute! In qualità di membri dell'ICI, ...
Rheonics Selezione dello strumento
Rheonics progetta, produce e commercializza sistemi innovativi di rilevamento e monitoraggio dei fluidioring sistemi. Precisione costruita in Svizzera, RheonicsI viscosimetri e i densimetri in linea hanno la sensibilità richiesta dall'applicazione e l'affidabilità necessaria per sopravvivere in un ambiente operativo difficile. Risultati stabili – anche in condizioni di flusso avverse. Nessun effetto della caduta di pressione o della portata. È ugualmente adatto alle misurazioni di controllo qualità in laboratorio. Non è necessario modificare alcun componente o parametro per misurare l'intero intervallo.
Prodotto / i suggerito / i per l'applicazione
- Ampia gamma di viscosità: monitora l'intero processo
- Misurazioni ripetibili in fluidi newtoniani e non newtoniani, fluidi monofase e multifase
- Parti a contatto con il fluido ermetiche 316L in acciaio inossidabile
- Misurazione della temperatura del fluido integrata
- Fattore di forma compatto per una semplice installazione in linee di processo esistenti
- Facile da pulire, nessuna manutenzione o riconfigurazione necessaria
- Strumento unico per la misura della densità di processo, viscosità e temperatura
- Misurazioni ripetibili in fluidi sia newtoniani che non newtoniani, fluidi monofase e multifase
- Costruzione interamente in metallo (acciaio inossidabile 316L)
- Misurazione della temperatura del fluido integrata
- Fattore di forma compatto per una semplice installazione in tubi esistenti
- Facile da pulire, nessuna manutenzione o riconfigurazione necessaria