Gli impianti di trattamento devono affrontare la sfida di normative più severe e standard più elevati per la qualità dell’acqua finita. I nuovi sviluppi nelle strategie di controllo e nella progettazione degli strumenti hanno superato alcune delle precedenti limitazioni di monitoring e controllare il processo di coagulazione. Un analizzatore di fiocchi online fornisce preziose informazioni sulla dinamica dell'aggregazione delle particelle dopo la coagulazione.
Ottimizzando la coagulazione si formerà un fiocco grande e facilmente depositabile. L'analisi frattale ha suggerito che la diffusione e la collisione di particelle colloidali limitano l'aggregazione delle particelle. Quindi, una corretta miscelazione è un fattore importante che influenza la formazione di fiocchi.
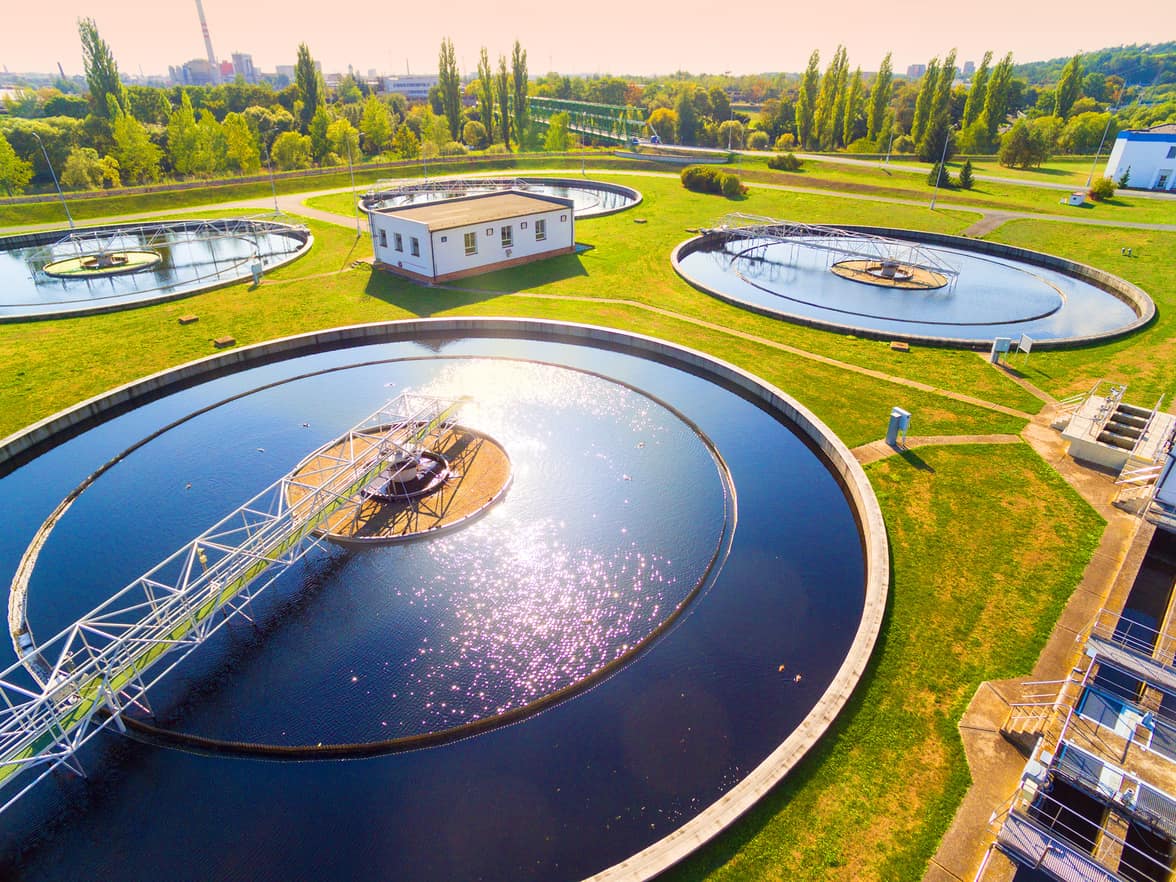
Applicazioni
La coagulazione è un processo essenziale per la rimozione di materiale in sospensione e colloidale dall'acqua e dalle acque reflue. La flocculazione in linea è una tecnica promettente per la disidratazione e la bonifica degli sterili di sabbie bituminose.
- Per pulire gli effluenti dell'industria e riciclarli per un ulteriore utilizzo
- Per ridurre l'uso di acqua dolce/potabile nelle industrie
- Per tagliare la spesa per l'approvvigionamento idrico
- Per soddisfare gli standard per l'emissione o lo scarico di inquinanti ambientali da vari settori stabiliti dal governo ed evitare pesanti sanzioni
- Per salvaguardare l'ambiente dall'inquinamento e contribuire allo sviluppo sostenibile
Cos'è la flocculazione?
La flocculazione è un processo di trattamento dell'acqua in cui i solidi formano ammassi più grandi, o fiocchi, da rimuovere dall'acqua. Questo processo può avvenire spontaneamente o con l'aiuto di agenti chimici. È un metodo comune per il trattamento delle acque piovane, il trattamento delle acque reflue e la purificazione dell'acqua potabile. Uno dei requisiti per l'acqua trattata in uscita dagli impianti di acque reflue è la rimozione dei solidi sospesi. Piccole particelle solide influiscono sul colore dell'acqua e trasportano le impurità nelle nostre fonti d'acqua naturali come i fiumi e l'oceano.
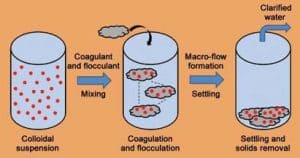
Coagulazione e flocculazione di una sospensione colloidale per aggiunta di un sistema coagulante-flocculante previa miscelazione con successiva decantazione del reticolo di fiocchi
Cosa sono i flocculanti?
I flocculanti sono composti che stimolano l'agglomerazione di minuscole particelle in una soluzione, determinando la formazione di un fiocco, che successivamente galleggia verso l'alto (flottazione) o affonda verso il basso (sedimentazione). Inoltre, questo può quindi essere estratto dal liquido più facilmente. I flocculanti inorganici e organici sono disponibili in una varietà di cariche, pesi molecolari, densità di carica e morfologie.
Conseguenze di una errata concentrazione delle acque reflue
Gli impianti di trattamento devono affrontare la sfida di normative più severe e standard più elevati per la qualità dell'acqua finita.
Senza la giusta concentrazione ci sono:
- possibilità di fallimento catastrofico
- impianto di trattamento bloccato (acque reflue)
- tubi congelati, esplosioni
- trattamento dell'acqua improprio
- l'acqua trattata in modo improprio viene scaricata portando a una sanzione elevata
I nuovi sviluppi nelle strategie di controllo e nella progettazione degli strumenti hanno superato alcune delle precedenti limitazioni di monitoring e controllare il processo di coagulazione. Un analizzatore di fiocchi online fornisce preziose informazioni sulla dinamica dell'aggregazione delle particelle dopo la coagulazione.
Ottimizzando la coagulazione si formerà un fiocco grande e facilmente depositabile. L'analisi frattale ha suggerito che la diffusione e la collisione di particelle colloidali limitano l'aggregazione delle particelle. Quindi, una corretta miscelazione è un fattore importante che influenza la formazione di fiocchi.
Settori:
Centrale elettrica, acciaio, raffinerie, industria mineraria, alimentare, zucchero, distilleria, elettronica, fertilizzanti, prodotti chimici, tessile, carta e polpa, cemento, ospitalità, commerciale, residenziale
applicazioni:
- Chiarificazione dell'acqua grezza
- Rimozione del colore
- Disidratazione dei fanghi
- De-oliare
- Applicazioni di processo industriale
Affinché gli impianti di trattamento dei rifiuti siano conformi a normative più rigorose e funzionino in modo sicuro ed efficiente, monitoring e sono richiesti sistemi di controllo con le seguenti caratteristiche:
- Può accogliere in modo flessibile le modifiche normative in monitoring soggetti e valori limite
- Monitoring e i punti di controllo possono essere facilmente aggiunti in ogni fase del processo
- Il monitoring e il sistema di controllo può far fronte in tempo reale a emergenze come lo scarico di effluenti tossici in un fiume in una località remota.
- Si integra perfettamente con un monitor centralizzatooring e sistema di controllo, consentendo l'integrazione dei processi di utilità e produzione
- Può funzionare con elevata affidabilità e stabilità per lunghi periodi di tempo
Polielettroliti - gli agenti di flocculazione
I polielettroliti sono flocculanti chimici utilizzati nel trattamento delle acque; agiscono principalmente nella fase di coagulazione-flocculazione e nel condizionamento/ispessimento della linea fanghi. I polielettroliti mostrano molte applicazioni in campi, come in trattamento delle acque come agenti di flocculazione, negli impasti ceramici come agenti disperdenti e negli impasti cementizi come superfluidificanti.
I polielettroliti sono polimeri organici a catena lunga spesso con pesi molecolari superiori a un milione e sono di origine naturale o sintetica. Il termine "polielettrolita" è stato introdotto per includere quei polimeri che, mediante un meccanismo di produzione di ioni, possono essere convertiti in una molecola polimerica avente cariche elettriche lungo la sua lunghezza. Le cariche elettriche derivano dalla presenza di gruppi funzionali ionizzabili lungo la catena polimerica. I polielettroliti sono, quindi, elettroliti polimerici, cioè aventi caratteristiche sia dei polimeri che degli elettroliti.
I polielettroliti commerciali utilizzati nell'aggregazione delle sostanze sospese sono solubili in acqua. Possono presentarsi in forme granulari, sotto forma di polvere o liquidi altamente viscosi. Tutti i polielettroliti esistenti hanno la tendenza a degradarsi se conservati per un periodo di tempo – Per un prodotto particolare, tale periodo è solitamente indicato dal produttore. In generale, più diluita è una soluzione di polielettrolita, più veloce è la degradazione, che probabilmente comporta la rottura delle lunghe catene, con conseguente diminuzione della viscosità.
Grado di utilizzazione dei polielettroliti
L'uso e l'importanza dei polielettroliti sta aumentando rapidamente. Anche il numero di produttori che producono questi materiali è in aumento. I polielettroliti sintetici hanno trovato notevoli applicazioni nelle seguenti vaste aree:
- Industrie di processo
- Trattamento delle acque reflue industriali
- Trattamento delle acque
- Trattamento delle acque reflue domestiche
I polielettroliti disponibili in commercio includono polidimetilammonio cloruro (PolyDADMAC), acido poliacrilico (PAA) e polistirene solfonato. I gradi commerciali di polielettroliti (PAA) sono disponibili presso Dow Chemical (Duramax, Tamol, Romax, Dowex), Rohm and Haas (Acusol, Acumer), BASF (Dispex®, Magnafloc®) e Arkema (Rheoslove, Terrablend). Gli usi specifici dei polielettroliti nelle industrie di processo includono la chiarificazione del succo di zucchero greggio nell'industria dello zucchero; separazione del gesso dall'acido fosforico a umido; miglioramento della sedimentazione nel funzionamento dell'idropulitrice; aumento della capacità dell'addensante nella produzione di cemento con processo a umido; separazione delle impurità argillose dai flussi di borace caldo; migliorare la qualità della deposizione di metalli nella raffinazione elettrolitica o nell'elettroestrazione di rame e zinco; miglioramento delle operazioni di ispessimento nella lavorazione dell'uranio, e così via. I polielettroliti possono essere utilizzati anche per il trattamento delle acque reflue industriali. La lotta all'inquinamento dei fiumi si fa sempre più intensa e le industrie hanno bisogno di tutto l'aiuto possibile. I polielettroliti stanno diventando un fattore sempre più importante nella risoluzione di questi problemi di inquinamento. In futuro, i polielettroliti avranno un impatto maggiore sul trattamento delle acque reflue industriali rispetto al trattamento delle acque reflue municipali. Ciò potrebbe essere dovuto al fatto che gli impianti di trattamento delle acque reflue industriali non sono soggetti agli stessi vincoli degli impianti di trattamento delle acque reflue municipali. Pertanto, i progettisti di impianti di trattamento dei rifiuti industriali potrebbero essere più concentrati sulla riduzione dei costi complessivi dell'impianto di trattamento che sul fatto che tali risparmi derivino da investimenti di capitale o costi operativi.
Sistemi di preparazione e dosaggio
Le poliacrilammidi sono polimeri ad altissimo peso molecolare grammo utilizzati come flocculanti. Questi polimeri sono disponibili principalmente sotto forma di polvere o emulsione. Possono essere anionici o cationici. Il principale svantaggio della flocculazione con polimeri è la finestra di flocculazione molto piccola, che rischia la risospensione delle particelle con pochi incrementi di dosaggio.
Alcuni di questi prodotti esistono sotto forma di soluzioni altamente viscose (da 5,000 a 10,000 centipoise) che possono essere pompate come fornite con diluizione secondaria alla mandata della pompa di alimentazione.
Il processo di preparazione si basa su tre fasi: dissoluzione, maturazione e trasferimento.
- Dissoluzione. Il polimero viene umidificato e sciolto per lenta agitazione, favorendo l'omogeneizzazione della soluzione.
- La soluzione viene mantenuta in continua e lenta agitazione.
- Le sonde di livello agiscono in modo che la soluzione possa essere dosata automaticamente al trattamento nido.
Con l'automazione il cliente potrà evitare interventi manuali, nonché errori nel dosaggio del prodotto. Questa apparecchiatura riesce ad integrare i polielettroliti in polvere nella soluzione per ottenere una corretta dispersione e performance degli stessi all'interno del processo di trattamento delle acque.
Le soluzioni di polielettroliti sono estremamente viscose e spesso sono necessarie solo dosi molto piccole. È quindi essenziale che vi sia sufficiente turbolenza nel punto di dosaggio per assicurare una rapida e completa miscelazione della piccola quantità di reagente con il flusso d'acqua principale. Le soluzioni di polielettrolita diluito sono più facili da disperdere nel flusso rispetto alle soluzioni concentrate, ma è necessario trovare un equilibrio altrimenti il volume della soluzione di polielettrolita aggiunta diventerà una proporzione significativa rispetto al flusso.
Unità di preparazione automatica: https://www.keiken-engineering.com/en/polyelectrolyte-preparation-equipment/
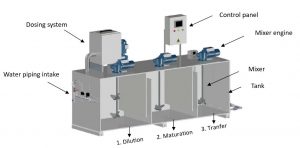
Unità di preparazione automatica (Rif: Keiken Engineering)
Diluizione in linea
Per garantire l'efficacia del polimero, sarà quasi sempre necessario diluire la soluzione preparata per ottenere a dispersione uniforme del polimero attraverso l'acqua o il fango precedentemente coagulato; pertanto, questa diluizione dipenderà dalla viscosità del polimero e del fango e dall'energia di miscelazione applicata al sistema. Di conseguenza, si applicheranno i seguenti livelli di diluizione target:
- da 5 a 1 g · L-1nel trattamento dei fanghi;
- da 02 a 0.1 g · L-1nel chiarimento.
Questa diluizione in linea viene effettuata sulla mandata della pompa dosatrice. Questa soluzione viene pompata nell'impianto di acque reflue, la soluzione viene utilizzata per depositare/coagulare i solidi nelle acque reflue. Quando la concentrazione di polielettrolita è sbagliata, possono essere rilasciate acque reflue che possono portare a sanzioni.
Esistono test su scala da banco e metodi di laboratorio per determinare la concentrazione:
- Versare la prova
- Prova di drenaggio per gravità
- Prova dell'elicottero
Tuttavia, questi metodi sono offline e ingombranti. Richiedono agli operatori di raccogliere un campione di fluido, analizzarlo separatamente e quindi prendere decisioni di processo. In confronto, i dispositivi in linea in grado di visualizzare le proprietà della miscela ed effettuare dosi corrette automatizzate sarebbero molto più efficienti, produttivi e ridurrebbero il consumo complessivo di polimero mediante il dosaggio esatto.
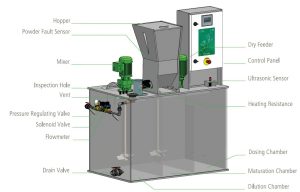
Sistemi di preparazione dei polimeri (Rif: PolySys CSL di Kozegho)
Viscosità – Indicatore dell'efficienza della soluzione polimerica
Il polimero è disponibile in tre forme diverse: secco, in soluzione (Mannich) e polimero in emulsione. La maggior parte dei polimeri utilizzati nelle industrie delle acque reflue sono a base di acrilammide e spesso chiamati PAAM (poliacrilammide).
I polimeri in emulsione utilizzati per i processi di separazione dei solidi sono idrolizzati, ad alto peso molecolare e hanno una viscosità molto elevata. Una delle caratteristiche più importanti dei polimeri in emulsione è la loro fluidità e gel polimerici di dimensioni micrometriche che consentono agli operatori di utilizzare sistemi di miscelazione/alimentazione di polimeri in linea. Sono costituiti da gel polimerici emulsionati in olio idrocarburico al 30%. A seconda del contenuto di acqua nei gel polimerici, il polimero attivo nel polimero in emulsione varia dal 20% al 55%. Pertanto, i polimeri in emulsione costano più del polimero secco su base per libbra. Il polimero consegnato a un sito è "pulito" e include acqua, olio, tensioattivi e polimero attivo. Tuttavia, il contenuto attivo è la porzione dell'emulsione che effettivamente condiziona i solidi nei processi a valle ed è il contenuto attivo che dovrebbe essere considerato quando si valutano le dosi di polimero appropriate per i sistemi di trattamento dei solidi. I polimeri in emulsione possono essere consegnati in piccoli fusti da 55 galloni, contenitori da 270 galloni o carichi di cisterne da 4000 a 5000 galloni.
Il concetto di miscelazione a due stadi è ben consolidato nel processo di trasformazione del polimero.
- Primo stadio: miscelazione ad altissima energia nella fase iniziale di bagnatura per prevenire la formazione di “fisheye”.
- Secondo stadio: miscelazione a bassa energia per ridurre al minimo il danneggiamento delle molecole polimeriche mentre si "svolgono" fuori dai gel/particelle polimeriche. Per la seconda fase è richiesto un tempo di residenza molto più lungo rispetto alla prima fase.
Quantità di attrito misurata dalla forza che resiste a un flusso in cui strati paralleli hanno una velocità unitaria l'uno rispetto all'altro. La scheda tecnica del fornitore di polimeri fornisce un punto di partenza per il fattore critico di viscosità per l'efficienza del polimero.
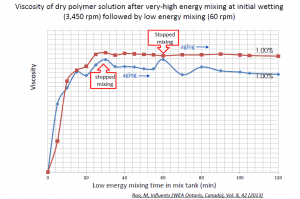
Viscosità vs tempo di miscelazione nella preparazione di polielettroliti (Rif: https://www.wef.org/globalassets/assets-wef/3—resources/online-education/webcasts/presentation-handouts/25june20-final-deck-handouts.pdf)
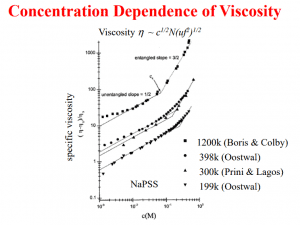
Dipendenza dalla concentrazione della viscosità (Rif: http://boulderschool.yale.edu/sites/default/files/files/Polyelectrolytes_Lecture_3.pdf )
Rheonics' soluzioni per sistemi di dosaggio di polielettroliti nel trattamento delle acque reflue
La misurazione e il controllo automatizzati della viscosità in linea sono fondamentali per controllare la viscosità durante il processo di produzione e garantire che le caratteristiche critiche siano pienamente conformi ai requisiti su più lotti, senza dover fare affidamento su metodi di misurazione offline e tecniche di prelievo di campioni. Rheonics offre le seguenti soluzioni per il controllo e l'ottimizzazione dei processi,
Misuratori di viscosità e densità
- In linea Viscosità misure: Rheonics' SRV è un dispositivo di misurazione della viscosità in linea ad ampia gamma in grado di rilevare i cambiamenti di viscosità all'interno di qualsiasi flusso di processo in tempo reale.
- In linea Viscosità e densità misure: Rheonics' SRD è uno strumento di misura simultanea di densità e viscosità in linea. Se la misurazione della densità è importante per le vostre operazioni, SRD è il miglior sensore per soddisfare le vostre esigenze, con capacità operative simili all'SRV insieme a misurazioni accurate della densità.
Integrato, chiavi in mano qualità gestione
Rheonics offre una soluzione integrata chiavi in mano per la gestione della qualità composta da:
- In linea Viscosità misure: Rheonics'SRV - un dispositivo di misurazione della viscosità in linea ad ampia gamma con misurazione della temperatura del fluido incorporata
- Rheonics Process Monitor: un avanzato controller di tracciamento predittivo monitorare e controllare in tempo reale le variazioni delle condizioni di processo
- Rheonics Reopulse con automaticamente in Sistemi dOsing: Un sistema autonomo di livello 4 che garantisce nessun compromesso con i limiti di viscosità impostati e attiva automaticamente le valvole o le pompe di by-pass per dosare in modo adattivo i componenti della miscela
Il sensore SRV si trova in linea, quindi misura continuamente la viscosità (e la densità in caso di SRD). Gli avvisi possono essere configurati per notificare all'operatore l'azione necessaria oppure l'intero processo di gestione può essere completamente automatizzato RTC (Rheonics Controller di monitoraggio predittivo). L'utilizzo di un SRV in una linea di processo di produzione comporta un miglioramento della produttività e dei margini di profitto e garantisce la conformità normativa. Rheonics i sensori hanno un fattore di forma compatto per una semplice installazione OEM e retrofit. Non richiedono manutenzione o riconfigurazioni. I sensori offrono risultati accurati e ripetibili indipendentemente da come o dove sono montati, senza necessità di camere speciali, guarnizioni in gomma o protezione meccanica. Non utilizzando materiali di consumo e non richiedendo ricalibrazione, SRV e SRD sono estremamente facili da utilizzare, con conseguenti costi di gestione estremamente bassi.
Una volta stabilito l’ambiente del processo, di solito è richiesto poco sforzo per mantenere l’integrità e la coerenza dei sistemi: gli operatori possono fare affidamento sullo stretto controllo con Rheonics soluzione di gestione della qualità della produzione.
Rheonics'Vantaggio
Fattore di forma compatto, nessuna parte mobile e nessuna manutenzione
Rheonics' SRV e SRD hanno un fattore di forma molto piccolo per una semplice installazione OEM e retrofit. Consentono una facile integrazione in qualsiasi flusso di processo. Sono facili da pulire e non richiedono manutenzione o riconfigurazioni. Hanno un ingombro ridotto che consente l'installazione in linea in qualsiasi linea di processo, evitando qualsiasi spazio aggiuntivo o necessità di adattatori.
Elevata stabilità e insensibilità alle condizioni di montaggio: qualsiasi configurazione possibile
Rheonics SRV e SRD utilizzano un esclusivo risonatore coassiale brevettato, in cui due estremità dei sensori ruotano in direzioni opposte, annullando le coppie di reazione sul loro montaggio e quindi rendendoli completamente insensibili alle condizioni di montaggio e alle portate. L'elemento sensore si trova direttamente nel fluido, senza requisiti di alloggiamento speciale o gabbia protettiva.
Letture accurate istantanee sulla qualità della produzione - Panoramica completa del sistema e controllo predittivo
RheonicsIl software è potente, intuitivo e comodo da usare. Il fluido di processo in tempo reale può essere monitorato sull'IPC integrato o su un computer esterno. Più sensori sparsi nell'impianto sono gestiti da un'unica dashboard. Nessun effetto della pulsazione della pressione derivante dal pompaggio sul funzionamento del sensore o sulla precisione della misurazione. Nessun effetto di vibrazione.
Misure in linea, non è necessaria alcuna linea di bypass
Installa direttamente il sensore nel tuo flusso di processo per eseguire misurazioni di viscosità (e densità) in tempo reale. Non è richiesta alcuna linea di bypass: il sensore può essere immerso in linea; la portata e le vibrazioni non influiscono sulla stabilità e l'accuratezza della misurazione.
Installazione semplice e nessuna riconfigurazione / ricalibrazione necessaria: zero manutenzione / tempi di fermo macchina
Nell'improbabile eventualità di un sensore danneggiato, sostituire i sensori senza sostituire o riprogrammare l'elettronica. Sostituzioni immediate sia per il sensore che per l'elettronica senza aggiornamenti del firmware o modifiche alla calibrazione. Montaggio facile. Disponibile con connessioni al processo standard e personalizzate come NPT, Tri-Clamp, DIN 11851, Flangia, Varinline e altri collegamenti sanitari e igienici. Nessuna camera speciale. Facilmente rimovibile per la pulizia o l'ispezione. SRV è disponibile anche con DIN11851 e tri-clamp connessione per un facile montaggio e smontaggio. Le sonde SRV sono sigillate ermeticamente per il Clean-in-place (CIP) e supportano il lavaggio ad alta pressione con connettori M69 IP12K.
Basso consumo energetico
Alimentazione 24 V CC con assorbimento di corrente inferiore a 0.1 A durante il normale funzionamento.
Tempi di risposta rapidi e viscosità compensata in temperatura
L'elettronica ultraveloce e robusta, combinata con modelli computazionali completi, rendono Rheonics dispositivi tra i più veloci, versatili e accurati del settore. SRV e SRD forniscono misurazioni accurate della viscosità (e della densità per SRD) in tempo reale ogni secondo e non sono influenzati dalle variazioni della portata!
Ampie capacità operative
RheonicsGli strumenti sono costruiti per effettuare misurazioni nelle condizioni più difficili.
SRV è disponibile con la più ampia gamma operativa nel mercato del viscosimetro di processo in linea:
- Range di pressione fino a 5000 psi
- Intervallo di temperatura da -40 fino a 200 ° C
- Intervallo di viscosità: 0.5 cP fino a 50,000 cP (e superiore)
SRD: strumento singolo, tripla funzione - Viscosità, temperatura e densità
Rheonics' SRD è un prodotto unico che sostituisce tre diversi strumenti per le misurazioni di viscosità, densità e temperatura. Elimina la difficoltà di collocare tre diversi strumenti e fornisce misurazioni estremamente accurate e ripetibili nelle condizioni più difficili.
Design e tecnologia dei sensori superiori
L'elettronica sofisticata e brevettata è il cervello di questi sensori. SRV e SRD sono disponibili con connessioni al processo standard del settore come ¾" NPT, DIN 11851, flangia e Tri-clamp consentendo agli operatori di sostituire un sensore di temperatura esistente nella linea di processo con un SRV/SRD che fornisce informazioni sui fluidi di processo estremamente preziose e utilizzabili come la viscosità oltre a una misurazione accurata della temperatura utilizzando un Pt1000 integrato (disponibile DIN EN 60751 Classe AA, A, B) .
Elettronica costruita per soddisfare le tue esigenze
Disponibile sia nella custodia del trasmettitore che in un montaggio su guida DIN di dimensioni ridotte, l'elettronica del sensore consente una facile integrazione nelle linee di processo e all'interno degli armadi delle apparecchiature delle macchine.
Facile da integrare
Molteplici metodi di comunicazione analogica e digitale implementati nell'elettronica del sensore rendono il collegamento a PLC industriali e sistemi di controllo semplici e diretti.
Opzioni di comunicazione analogica e digitale
Opzioni di comunicazione digitale opzionali
Conformità ATEX e IECEx
Rheonics offre sensori a sicurezza intrinseca certificati ATEX e IECEx per l'uso in ambienti pericolosi. Questi sensori sono conformi ai requisiti essenziali di salute e sicurezza relativi alla progettazione e costruzione di apparecchiature e sistemi di protezione destinati all'uso in atmosfere potenzialmente esplosive.
Le certificazioni di sicurezza intrinseca e antideflagrante possedute da Rheonics consente inoltre la personalizzazione di un sensore esistente, consentendo ai nostri clienti di evitare i tempi e i costi associati all'identificazione e al test di un'alternativa. Possono essere forniti sensori personalizzati per applicazioni che richiedono da una unità fino a migliaia di unità; con tempi di consegna di settimane anziché di mesi.
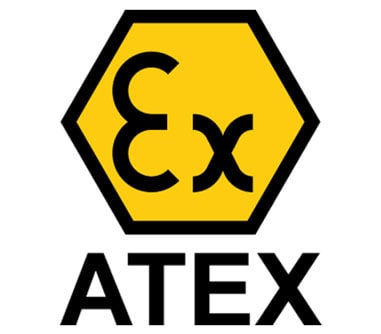
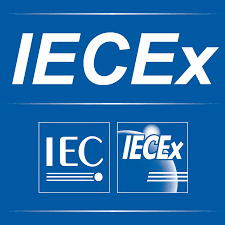
Rheonics Selezione dello strumento
Rheonics progetta, produce e commercializza sistemi innovativi di rilevamento e monitoraggio dei fluidioring sistemi. Precisione costruita in Svizzera, RheonicsI viscosimetri e i densimetri in linea hanno la sensibilità richiesta dall'applicazione e l'affidabilità necessaria per sopravvivere in un ambiente operativo difficile. Risultati stabili – anche in condizioni di flusso avverse. Nessun effetto della caduta di pressione o della portata. È ugualmente adatto alle misurazioni di controllo qualità in laboratorio. Non è necessario modificare alcun componente o parametro per misurare l'intero intervallo.
Prodotto / i suggerito / i per l'applicazione
- Ampia gamma di viscosità: monitora l'intero processo
- Misurazioni ripetibili in fluidi newtoniani e non newtoniani, fluidi monofase e multifase
- Parti a contatto con il fluido ermetiche 316L in acciaio inossidabile
- Misurazione della temperatura del fluido integrata
- Fattore di forma compatto per una semplice installazione in linee di processo esistenti
- Facile da pulire, nessuna manutenzione o riconfigurazione necessaria
- Strumento unico per la misura della densità di processo, viscosità e temperatura
- Misurazioni ripetibili in fluidi sia newtoniani che non newtoniani, fluidi monofase e multifase
- Costruzione interamente in metallo (acciaio inossidabile 316L)
- Misurazione della temperatura del fluido integrata
- Fattore di forma compatto per una semplice installazione in tubi esistenti
- Facile da pulire, nessuna manutenzione o riconfigurazione necessaria