Introduzione
I polimeri sono passati dall'essere sostituti economici dei prodotti naturali alla fornitura di opzioni di alta qualità per una varietà di applicazioni industriali a causa del loro basso costo, gamma di proprietà (elevata resistenza chimica, resistenza alle alte temperature, alto rapporto resistenza-peso) e facilità di elaborazione. Sono utilizzati come imballaggi per pellicole forme stampate solide per parti di carrozzeria di automobili, cabine TV, parti di aeromobili, schiume per tazze di caffè e isolamento del frigorifero, fibre per indumenti e tappeti, adesivi, gomma per pneumatici e tubi, vernici e altri rivestimenti e molti altre applicazioni.
L'estrusione di polimeri richiede un consumo energetico estremamente elevato e il monitoraggio in tempo realeoring del consumo di energia e della qualità della fusione è diventato estremamente necessario per soddisfare le nuove normative sul carbonio e sopravvivere nel mercato altamente competitivo della plastica.
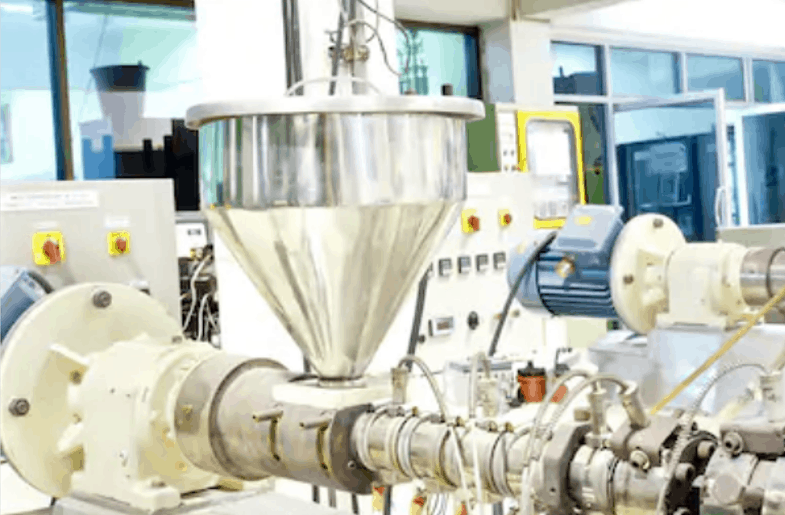
Applicazioni
I polimeri subiscono stampaggio ad iniezione, stampaggio a compressione o estrusione - tutti elementi che richiedono la forzatura di un polimero in una forma. L'elaborazione è tuttavia ad alta intensità energetica. Nel Regno Unito, i costi dell'elettricità per la lavorazione della plastica ammontano a circa £ 350 milioni all'anno. Una riduzione del consumo di elettricità comporterebbe enormi risparmi e una significativa riduzione degli oneri ambientali.
L'energia consumata durante la lavorazione dei polimeri può essere suddivisa in due aspetti: il sistema di gestione dell'energia di alto livello e il controllo dei macchinari di basso livello. Per il sistema di gestione energetica di alto livello, è possibile ottenere una riduzione del consumo energetico di circa 30% attraverso la gestione e la manutenzione del processo. Senza la corretta gestione del processo, impostazioni operative non ottimali come il riscaldamento termico, il raffreddamento e la velocità di elaborazione in caso di processo di estrusione di polimeri contribuiscono a un enorme spreco di energia.
La densità e la viscosità dei polimeri fusi sono parametri fisico-chimici molto importanti in un processo di fabbricazione di polimeri. Sono fattori molto significativi che incidono sul costo di produzione e sulla redditività del processo di fabbricazione. I polimeri subiscono stampaggio ad iniezione, stampaggio a compressione o estrusione - tutti elementi che richiedono la forzatura di un polimero in una forma.
La caratterizzazione in linea dei materiali sta mostrando una crescente popolarità tra i ricercatori che lavorano per migliorare le prestazioni di molti processi di produzione esistenti e nuovi processi. I vantaggi associati all'applicazione di queste tecniche possono essere direttamente correlati al miglioramento della qualità e alla riduzione dei costi di produzione. Le misure di reologia possono essere utilizzate per la caratterizzazione del materiale, la determinazione della processabilità e come dati di input per simulazioni al computer. La reologia presenta vantaggi rispetto ad altri metodi a causa della sua sensibilità a determinati aspetti della struttura come coda e ramificazione ad alto peso molecolare. In molti casi, la caratterizzazione reologica è molto più veloce delle sue controparti.
Nel processo di estrusione, la densità del prodotto è il fattore più critico che influenza i costi di produzione e la redditività complessiva del processo di fabbricazione. Una riduzione della densità riduce i costi delle materie prime. Tuttavia, se la densità del prodotto viene mantenuta troppo bassa, degrada le proprietà meccaniche e l'accuratezza geometrica. Pertanto, un equilibrio critico è essenziale al fine di ridurre i costi dei materiali, mantenendo allo stesso tempo resistenza e precisione adeguate. La densità della schiuma di PVC può essere controllata variando il tipo e la quantità di additivi composti, i parametri di lavorazione (temperatura, velocità della vite) o entrambi.
Lo scopo principale della regolazione continua delle impostazioni operative è garantire una qualità di fusione costante. La ricerca ha dimostrato che la viscosità del fuso è probabilmente il miglior indicatore della qualità del fuso (Cogswell, 1981). Per materiali più viscosi, è necessario fornire maggiore forza e regolare altre condizioni, come la temperatura. I produttori devono comprendere attentamente queste informazioni per garantire condizioni adeguate e il miglior utilizzo delle risorse. Per ottimizzare le impostazioni operative, un monitoraggio in tempo realeoring è richiesta la viscosità del fuso.
Le sfide
L'estrusione a vite singola e doppia è la tecnica di estrusione più utilizzata. I granuli di plastica vengono spinti da una vite che si sposta dalla zona di alimentazione allo stampo e i granuli si sciolgono con il calore dovuto allo sforzo di taglio e al riscaldamento della canna.
Relativo all'applicazione
La maggior parte dei materiali polimerici presenta un comportamento estremamente complicato, in particolare in caso di fusione di polimeri. L'applicazione richiede misurazioni in condizioni molto difficili - ad alta pressione (50-100 MPa) e alte temperature (circa 150-300 ° C). In HPHT esiste un alto rischio di problemi di accuratezza e affidabilità.
Problemi con il monitoraggio del processooring con il consumo di energia del motore
Poche aziende di lavorazione della plastica monitorano il consumo di energia del motore dell'estrusore per studiare la stabilità del fuso, la qualità del prodotto finale e anche l'efficienza energetica. Tuttavia, ci sono alcune sfide con questa tecnica:
- L'installazione di misuratori di potenza per ciascun estrusore è costosa e modelli matematici basati sulle impostazioni di processo potrebbero rappresentare un'alternativa migliore
- I modelli esistenti dipendono fortemente dalla geometria dell'estrusore e dei materiali polimerici, è difficile utilizzare lo stesso modello su diversi casi d'uso senza riqualificazione
Problemi con il monitoraggio del processooring con pressione di fusione
Nel settore, la pressione di fusione vicino alla punta della vite è generalmente accettata come indicatore principale della qualità della fusione. Poche limitazioni con questa tecnica:
- È noto che la pressione è proporzionale alla velocità della vite, tuttavia è anche leggermente influenzata dalla temperatura di fusione, dalla geometria della vite e dal materiale polimerico in lavorazione.
- La pressione di fusione instabile provoca fluttuazioni della produttività e variazioni nella qualità del prodotto finale.
Limitazioni delle tradizionali tecniche di misurazione della viscosità
Il comportamento reologico della maggior parte dei materiali polimerici è piuttosto complesso. La viscosità dipende sia dal taglio che dalla storia termica. Spesso, la viscosità del polimero viene misurata off-line. Un campione di composto polimerico viene fuso e inserito in uno speciale tubo capillare (viscosimetro in vetro) o incorporando un tubo capillare montato parallelamente all'estrusore in caso di misurazioni online. Entrambe le tecniche comportano lunghi ritardi derivanti dal tempo necessario al flusso per fondere attraverso le linee di transito e il capillare. In alcuni casi, i viscosimetri sono montati sulle linee di estrusione che misurano la sollecitazione sulla parete dello stampo misurando la caduta di pressione lungo una fessura o un capillare e la portata viene misurata da un flussimetro supplementare. Sebbene questi metodi producano misurazioni della viscosità più rilevanti per il processo di estrusione, il flussometro spesso disturba il flusso di fusione alterando così le caratteristiche di flusso originali.
I viscosimetri meccanici ed elettromeccanici convenzionali progettati principalmente per misurazioni di laboratorio sono difficili da integrare nel controllo e nel monitoraggiooring ambiente. L'attuale metodologia di test nei laboratori fuori sede non è ottimale ed è costosa a causa delle sfide logistiche della spedizione e degli elevati costi fissi. I complessi cambiamenti che avvengono all'interno di un motore o di un compressore spesso non possono essere determinati da un campione di olio di routine perché i dati rappresentati da tale campione riflettono semplicemente un'istantanea delle condizioni dell'olio al momento del prelievo del campione e la strumentazione convenzionale può essere influenzata da velocità di taglio, temperatura e altre variabili.
Perché la misurazione della reologia online in tempo reale è importante?
Il monitoraggio online della viscosità in tempo reale offre numerosi vantaggi motivazionali dal punto di vista dei costi, dell'ambiente e della logistica.oring nel processo di produzione dei polimeri. È uno strumento eccellente per la caratterizzazione dei materiali e vari scopi di risoluzione dei problemi. I principali vantaggi sono i seguenti:
Vantaggi economici e logistici, riduzione dei costi di produzione: L'analisi della viscosità on-line ridurrebbe il numero di campioni inviati a laboratori fuori sede e i relativi costi. I risultati continui delle analisi in loco ridurrebbero inoltre la manodopera / i costi di spedizione e l'errore di campionamento.
Le misurazioni di reologia possono aiutare a risolvere i problemi durante l'elaborazione del polimero e ridurre gli errori:
- Pelle di squalo: I materiali che non sono molto diradati sono inclini alla pelle di squalo a velocità di produzione relativamente inferiori. Le informazioni sulla viscosità del materiale alla temperatura di lavorazione (nella regione del labbro) possono essere essenziali per ridurre lo stress da taglio, aumentare la temperatura dello stampo o utilizzare additivi che promuovono lo scivolamento e evitano il difetto.
- Instabilità delle bolle nel soffiaggio del film: Una bassa resistenza alla fusione del materiale può causare questo difetto. I valori di viscosità estensiva e / o resistenza alla fusione dei materiali possono essere utilizzati per confrontare la stabilità delle bolle di materiali diversi e scegliere il materiale giusto per l'applicazione. Il raffreddamento può aiutare a ridurre la temperatura delle bolle e quindi ad aumentare la forza di fusione.
- Scarsa miscelazione di due polimeri: Quando la differenza di viscosità tra due polimeri da miscelare è grande (ad es. Per tempi 5), la miscelazione è estremamente difficile perché la sollecitazione di taglio esercitata dalla matrice sulla fase dispersa con viscosità più elevata non è abbastanza grande da causare rotture. L'azione correttiva sarebbe quella di utilizzare una matrice di viscosità più elevata.
Migliore qualità del prodotto finale: Le misurazioni reologiche della materia prima e del prodotto finale possono caratterizzare le proprietà del prodotto come resistenza agli urti, aspetto ottico, deformazione, fragilità ecc. Monitoraggio continuooring può aiutare a rilevare qualsiasi modifica o degrado che potrebbe verificarsi durante il processo di estrusione.
Ridotto consumo di energia: Per ottimizzare le impostazioni operative, un monitoraggio in tempo realeoring è richiesta la viscosità del fuso. L'uso ottimale delle risorse e dell'elettricità nella produzione con uno stretto controllo sui processi è garantito grazie alle misurazioni reologiche in linea in tempo reale.
Maggiore sicurezza dei lavoratori: Altri fattori come i requisiti di salute e sicurezza per lavorare con i solventi, la considerazione per l'ambiente e la necessità per il personale specializzato di eseguire questi test (che devono essere eseguiti in laboratorio) aumentano la popolarità del metodo privo di solventi.
Tempi di risposta più rapidi: L'analisi della viscosità (e della densità) in situ ridurrebbe / eliminerebbe il ritardo tra il campionamento e la ricezione di una risposta dal laboratorio.
Ambiente: L'utilizzo delle risorse può essere massimizzato attraverso il monitoraggio on-lineoring sistemi, con conseguente riduzione degli sprechi, a vantaggio dell’ambiente. Maggiore sostenibilità grazie alla riduzione delle emissioni.
Rheonics' Soluzioni
La misurazione automatizzata e in tempo reale della viscosità in linea è fondamentale per la produzione di polimeri. Rheonics offre le seguenti soluzioni, basate su un risonatore torsionale bilanciato, per il controllo e l'ottimizzazione del processo nella lavorazione dei polimeri:
- In linea Viscosità misure: Rheonics' SRV è un dispositivo di misurazione della viscosità in linea ad ampio raggio con misurazione della temperatura del fluido integrata ed è in grado di rilevare in tempo reale le variazioni di viscosità all'interno di qualsiasi flusso di processo.
- In linea Viscosità e densità misure: Rheonics' SRD è uno strumento di misurazione simultanea in linea di densità e viscosità con misurazione della temperatura del fluido integrata. Se la misurazione della densità è importante per le tue operazioni, SRD è il sensore migliore per soddisfare le tue esigenze, con capacità operative simili all'SRV e misurazioni accurate della densità.
La misurazione automatizzata della viscosità in linea tramite SRV o SRD elimina le variazioni nelle tecniche di prelievo dei campioni e di laboratorio utilizzate per la misurazione della viscosità con i metodi tradizionali. Il sensore è posizionato in linea in modo da misurare continuamente la viscosità (e la densità in caso di SRD). Utilizzo di un SRV/SRD per il monitoraggio del processooring possono migliorare la produttività e aumentare i margini di profitto. Entrambi i sensori hanno un fattore di forma compatto per una semplice installazione OEM e retrofit. Non richiedono manutenzione o riconfigurazioni. Entrambi i sensori offrono risultati accurati e ripetibili indipendentemente da come o dove sono montati, senza necessità di camere speciali, guarnizioni in gomma o protezione meccanica. Non utilizzando materiali di consumo, SRV e SRD sono estremamente facili da utilizzare.
Fattore di forma compatto, nessuna parte mobile e nessuna manutenzione
Rheonics' SRV e SRD hanno un fattore di forma molto piccolo per una semplice installazione OEM e retrofit. Consentono una facile integrazione in qualsiasi flusso di processo. Sono facili da pulire e non richiedono manutenzione o riconfigurazioni. Hanno un ingombro ridotto che consente l'installazione in linea in qualsiasi linea di processo, evitando qualsiasi spazio aggiuntivo o necessità di adattatori.
Elevata stabilità e insensibilità alle condizioni di montaggio: qualsiasi configurazione possibile
Rheonics SRV e SRD utilizzano un esclusivo risonatore coassiale brevettato, in cui due estremità dei sensori ruotano in direzioni opposte, annullando le coppie di reazione sul loro montaggio e quindi rendendoli completamente insensibili alle condizioni di montaggio e alle portate. Questi sensori possono facilmente far fronte a spostamenti regolari. L'elemento sensore si trova direttamente nel fluido, senza la necessità di un alloggiamento speciale o di una gabbia protettiva.
Letture accurate istantanee delle condizioni di processo - Panoramica completa del sistema e controllo predittivo
RheonicsIl software è potente, intuitivo e comodo da usare. La viscosità in tempo reale può essere monitorata su un computer. Più sensori vengono gestiti da un unico dashboard distribuito in tutta la fabbrica. Nessun effetto della pulsazione della pressione derivante dal pompaggio sul funzionamento del sensore o sulla precisione della misurazione. Non influenzato da urti, vibrazioni o condizioni di flusso.
Installazione semplice e nessuna riconfigurazione / ricalibrazione necessaria
Sostituisci i sensori senza sostituire o riprogrammare l'elettronica, sostituzioni immediate sia per il sensore che per l'elettronica senza aggiornamenti del firmware o modifiche del coefficiente di calibrazione. Montaggio facile. Si avvita nella filettatura NPT da ¾" nel raccordo della linea dell'inchiostro. Nessuna camera, O-ring guarnizioni o guarnizioni. Facilmente rimovibile per la pulizia o l'ispezione. SRV disponibile con flangia e tri-clamp connessione per un facile montaggio e smontaggio.
Basso consumo energetico
Alimentatore CC 24V con assorbimento di corrente inferiore a 0.1 durante il normale funzionamento
Tempi di risposta rapidi e viscosità compensata in temperatura
L'elettronica ultraveloce e robusta, combinata con modelli computazionali completi, rendono Rheonics dispositivi uno dei più veloci e precisi del settore. SRV e SRD forniscono misurazioni accurate della viscosità (e della densità per SRD) in tempo reale ogni secondo e non sono influenzati dalle variazioni della portata!
Ampie capacità operative
RheonicsGli strumenti sono costruiti per effettuare misurazioni nelle condizioni più difficili. SRV ha la più ampia gamma operativa sul mercato dei viscosimetri da processo in linea:
- Range di pressione fino a 5000 psi
- Intervallo di temperatura da -40 fino a 200 ° C
- Intervallo di viscosità: 0.5 cP fino a 50,000 cP
SRD: strumento singolo, tripla funzione - Viscosità, temperatura e densità
Rheonics' SRD è un prodotto unico che sostituisce tre diversi strumenti per le misurazioni di viscosità, densità e temperatura. Elimina la difficoltà di collocare tre diversi strumenti e fornisce misurazioni estremamente accurate e ripetibili nelle condizioni più difficili.
Clean in place (CIP)
SRV (e SRD) monitora la pulizia delle linee tramite monitoring la viscosità (e densità) del solvente durante la fase di pulizia. Eventuali piccoli residui vengono rilevati dal sensore, consentendo all'operatore di decidere quando la linea è pulita allo scopo. In alternativa, SRV fornisce informazioni al sistema di pulizia automatizzato per garantire una pulizia completa e ripetibile tra un ciclo e l'altro, a differenza del caso dei capillari in vetro.
Design e tecnologia dei sensori superiori
L'elettronica sofisticata e brevettata di terza generazione guida questi sensori e valuta la loro risposta. SRV e SRD sono disponibili con connessioni al processo standard del settore come ¾" NPT e 3" Tri-clamp consentendo agli operatori di sostituire un sensore di temperatura esistente nella linea di processo con un SRV/SRD che fornisce informazioni sui fluidi di processo estremamente preziose e utilizzabili come la viscosità oltre a una misurazione accurata della temperatura utilizzando un Pt1000 integrato (disponibile DIN EN 60751 Classe AA, A, B) .
Elettronica costruita per soddisfare le tue esigenze
Disponibile sia in un alloggiamento del trasmettitore antideflagrante che in un montaggio su guida DIN con fattore di forma ridotto, l'elettronica del sensore consente una facile integrazione nelle tubazioni di processo e all'interno degli armadi delle macchine.
Facile da integrare
Molteplici metodi di comunicazione analogica e digitale implementati nell'elettronica del sensore rendono il collegamento a PLC industriali e sistemi di controllo semplici e diretti.
Conformità ATEX e IECEx
Rheonics offre sensori a sicurezza intrinseca certificati ATEX e IECEx per l'uso in ambienti pericolosi. Questi sensori sono conformi ai requisiti essenziali di salute e sicurezza relativi alla progettazione e costruzione di apparecchiature e sistemi di protezione destinati all'uso in atmosfere potenzialmente esplosive.
Le certificazioni di sicurezza intrinseca e antideflagrante possedute da Rheonics consente inoltre la personalizzazione di un sensore esistente, consentendo ai nostri clienti di evitare i tempi e i costi associati all'identificazione e al test di un'alternativa. Possono essere forniti sensori personalizzati per applicazioni che richiedono da una unità fino a migliaia di unità; con tempi di consegna di settimane anziché di mesi.
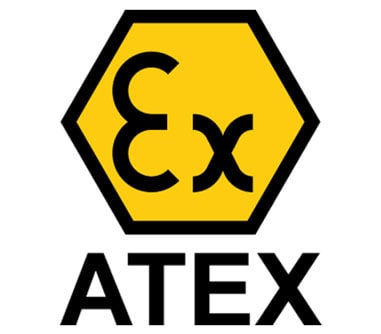
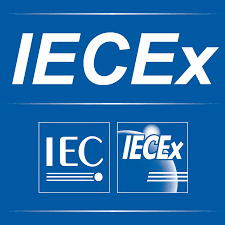
Implementazione
Installa direttamente il sensore nel tuo flusso di processo per eseguire misurazioni di viscosità e densità in tempo reale. Non è necessaria alcuna linea di bypass: il sensore può essere immerso in linea, la portata e le vibrazioni non influiscono sulla stabilità e l'accuratezza della misurazione. Ottimizza il processo decisionale fornendo test ripetuti, consecutivi e coerenti sul fluido.
Rheonics Selezione dello strumento
Rheonics progetta, produce e commercializza sistemi innovativi di rilevamento e monitoraggio dei fluidioring sistemi. Precisione costruita in Svizzera, Rheonics' viscosimetri in linea ha la sensibilità richiesta dall'applicazione e l'affidabilità necessaria per sopravvivere in un ambiente operativo difficile. Risultati stabili – anche in condizioni di flusso avverse. Nessun effetto della caduta di pressione o della portata. È ugualmente adatto alle misurazioni di controllo qualità in laboratorio.
Prodotto / i suggerito / i per l'applicazione
• Ampia gamma di viscosità: monitorare l'intero processo
• Misurazioni ripetibili in fluidi newtoniani e non newtoniani, fluidi monofase e multifase
• Costruzione interamente in metallo (acciaio inossidabile 316L)
• Misura della temperatura del fluido integrata
• Fattore di forma compatto per una semplice installazione in linee di processo esistenti
• Facile da pulire, nessuna manutenzione o riconfigurazione necessaria
• Strumento unico per la misura della densità, viscosità e temperatura del processo
• Misurazioni ripetibili in fluidi newtoniani e non newtoniani, fluidi monofase e multifase
• Costruzione interamente in metallo (acciaio inossidabile 316L)
• Misura della temperatura del fluido integrata
• Fattore di forma compatto per una semplice installazione in tubi esistenti
• Facile da pulire, nessuna manutenzione o riconfigurazione necessaria