Principali vantaggi della gestione della viscosità nelle linee di riempimento di prodotti liquidi:
- Operazioni della linea di confezionamento accurate ed efficienti: risparmi significativi sui costi dei materiali
- Cambio di prodotto senza soluzione di continuità: agilità nell'affrontare diverse e nuove varianti di prodotto e provenienza del prodotto
- Rispetto delle normative
- Ottimizzazione dei sistemi CIP
Introduzione
Il liquido di confezionamento, il liquido con pezzi solidi e i prodotti simili al gel sono costituiti dai materiali di imballaggio e dalle macchine di confezionamento come le linee di riempimento. Comprende formati di imballaggi rigidi come bottiglie e contenitori e formati di imballaggi flessibili come film, buste stand-up, tubi spremibili, cartoni e bag-on-box. In molti settori, i processi di confezionamento sono automatizzati utilizzando linee di riempimento.
Le aree di applicazione dell'imballaggio di liquidi abbracciano più settori: alimenti e bevande, cosmetici, prodotti per la casa, prodotti chimici, medicinali, prodotti di largo consumo. Alcuni esempi per settore sono:
- Alimenti e bevande: salse, latticini, succhi, bevande gassate, zuppe, caffè / tè, yogurt, latte, gelati, dessert di gelatina, miele, gelatina, sciroppi, cibo asettico, burro, burro chiarificato, birra ecc.
- Cosmetici: creme, lozioni, shampoo, viso, oli per capelli, filtri solari
- Medicinali: sciroppi, gocce, unguenti
- FMCG: dentifrici, disinfettanti, liquidi per il lavaggio delle mani, liquidi per piatti, detersivi liquidi
- Prodotti chimici: industriale, trattamento delle acque, adesivi, estrazione mineraria, catalizzatore, laboratorio e altri usi applicativi.
Meccanismi di riempimento / confezionamento
Una delle chiavi per una linea di confezionamento di liquidi di successo è l'efficienza. Per ottimizzare l'efficienza di una linea di confezionamento, ci sono molteplici fattori da considerare. Comprende la viscosità del liquido, le caratteristiche del prodotto, le sfide specifiche del prodotto, la facilità di pulizia, l'accuratezza, la facilità di flessibilità e sostituzione e l'utilizzo di un fornitore di macchine affidabile.
Tutti i liquidi fluiscono in modo diverso. Comprenderlo è della massima importanza durante la progettazione di una macchina riempitrice. La viscosità è la proprietà che fornisce informazioni sul comportamento del flusso del liquido. Pertanto, è fondamentale prendere nota della viscosità del prodotto che stai manipolando. I metodi di riempimento differiscono per costo, precisione, velocità e igiene. Non tutti i metodi sono adatti a tutti i liquidi, poiché le bevande richiedono un'igiene particolare, i cosmetici costosi richiedono una precisione speciale, mentre l'olio motore ha una caratteristica di flusso diversa, ad esempio, dall'acqua minerale. Un prodotto a flusso libero come l'acqua a bassa viscosità scorrerà bene attraverso un riempitivo a gravità. Questo perché questo tipo di macchina fa affidamento sulla forza di gravità per far passare il prodotto.
Alcuni prodotti che hanno una viscosità più alta necessitano di assistenza per essere inseriti nella confezione. Lozioni e altri liquidi ad alta viscosità funzionano bene con riempitivi a pistone e riempitivi a pompa. Le riempitrici a pistone hanno una capacità versatile di gestire liquidi da prodotti aerati a glasse e salse. Le riempitrici a pompa funzionano bene con liquidi di tutte le viscosità e offrono varietà quando si tratta della pompa scelta. Le pompe di riempimento possono utilizzare pompe a cavità progressiva, pompe a ingranaggi, pompe di lubrificazione e varie valvole e raccordi per soddisfare le esigenze del progetto.
Cosa rende l'automazione e il controllo della viscosità così importanti nella costruzione di una linea di confezionamento efficiente per prodotti liquidi?
Uno dei primi aspetti di una linea di confezionamento che un'azienda deve considerare è la viscosità del liquido che attraversa i processi di riempimento e confezionamento. Lo spessore del liquido sarà un fattore determinante quando si tratta di selezionare il macchinario giusto da acquistare e installare. Se l'attrezzatura viene utilizzata per il livello di viscosità sbagliato, ciò potrebbe ostacolare significativamente la produttività ed è più probabile che si verifichino guasti. Considerare se il liquido è liquido, più denso o altamente viscoso, cosa che può essere determinata utilizzando una viscosità chart nella scelta dei macchinari.
Il monitoraggio della viscosità in linea e in tempo reale offre numerosi vantaggioring e controllo in linea di confezionamento per prodotti fluidi/liquidi:
Operazioni della linea di confezionamento accurate ed efficienti - notevole risparmio sui costi dei materiali Il controllo della viscosità rende le linee di confezionamento dei liquidi più "accurate" garantendo un prodotto coerente e quindi consente un controllo più stretto per l'erogazione del giusto livello di prodotto. Il controllo della qualità della viscosità nelle fasi di produzione e trasporto, che precedono le operazioni di riempimento, può garantire che venga erogata l'esatta quantità di liquido, con quantità minime di variabilità di processo che possono eventualmente derivare dalle apparecchiature della linea di confezionamento come ugelli e valvole. Ciò si traduce in un significativo risparmio di materiale per l'azienda, considerando la portata delle operazioni.
Per rispettare le normative che penalizzano il riempimento insufficiente, durante la produzione i produttori spesso superano la quantità minima di imballaggi. Tuttavia, tale riempimento eccessivo di sicurezza può essere costoso. Ad esempio, un produttore di latte di medie dimensioni riempie circa 100,000 bottiglie di latte di cocco al giorno. Riducendo di pochi grammi il troppo pieno nelle singole bottiglie, l'azienda potrebbe potenzialmente risparmiare diversi milioni di euro all'anno. I produttori di impianti di imbottigliamento completi dovrebbero quindi offrire sistemi che misurino le quantità di riempimento con alta precisione e mantengano il riempimento eccessivo al minimo assoluto.
Cambio di prodotto senza interruzioni: agilità nell'affrontare diverse e nuove varianti di prodotto e provenienza del prodotto. Gli ingegneri di fabbrica ottengono un quadro più accurato di come reagiranno le nuove formulazioni o le modifiche alle ricette e di come potrebbe essere necessario regolare i sistemi attuali e i parametri di controllo. Monitoraggio in tempo realeoring facilita la transizione da un processo basato su batch al funzionamento continuo, risparmiando significativi costi operativi e di capitale attraverso il riutilizzo delle stesse linee per più prodotti. Gli ingegneri della linea di confezionamento possono rispondere rapidamente alle mutevoli richieste dei consumatori, ottimizzare la produzione e ridurre i costi di sistema.
Fonte: Pepsico Inc.
I dati sulla viscosità aiutano gli ingegneri della linea di confezionamento a regolare i parametri per garantire che mantengano uno stretto controllo del processo di erogazione non influenzato dal cambiamento delle proprietà del prodotto, in particolare la fluidità che dipende dalla viscosità. Inoltre, le decisioni di adattare i parametri e le variabili della macchina (ugelli, pompe, controlli delle valvole) possono essere guidate e automatizzate in modo affidabile dai dati di viscosità, garantendo così che il tempo di cambio sia limitato al minimo.
Conformità alle normative. Quando si tratta di prodotti alimentari e bevande, qualità, sicurezza e fiducia sono assolutamente fondamentali. La precisione e la ripetibilità del processo di dispensazione devono essere strettamente controllate, poiché le norme UE, OMS e altre linee guida GMP stabiliscono i livelli di tolleranza consentiti a seconda dei tipi di prodotto / settore. La sfida per tutti questi processi è la stessa: l'imballaggio deve contenere la quantità di prodotto dichiarata. Se la quantità di riempimento in bottiglie è troppo bassa, ad esempio, ciò viola la direttiva UE sul preconfezionamento 76/211 / CEE e la legge tedesca sui prodotti preconfezionati (§22 FPackV). Questi stabiliscono la percentuale in base alla quale un lotto di produzione può essere inferiore alla quantità di riempimento minima specificata. In questo caso, "cattiva condotta" può portare a sanzioni che includono l'arresto della produzione.
Ciò significa che l'automazione della viscosità è fondamentale per garantire che il processo di riempimento rimanga efficiente per evitare rischi di scarti, scarti e sanzioni, che possono essere significativamente alti nelle fabbriche di riempimento continuo di liquidi che imballano tonnellate di materiali ogni ora!
Altro Considerazioni sull'efficienza di a liquido linea di confezionamento
Facilità di pulizia. Un altro aspetto importante è la capacità di pulire l'attrezzatura facilmente e senza problemi. Più il macchinario è facile da pulire, meno tempo è necessario per pulire parti e macchine e più velocemente può essere di nuovo operativo. Macchinari facili da smontare contribuiranno a mantenere efficiente il processo di pulizia. Un esempio è che il cliente acquista un'apparecchiatura che offre una pulizia manuale o automatica (CIP), che è il modo più efficiente per pulire una riempitrice. Il CIP farà circolare la soluzione detergente attraverso la macchina per garantire che tutte le parti bagnate siano pulite.
Fonte immagine: TetraPak
Facilità di flessibilità, cambiamento e scalabilità. La facilità di cambio formato e la flessibilità dei macchinari sono anche parte integrante di un sistema di confezionamento efficiente. Ciò significa che l'apparecchiatura dovrebbe essere in grado di ospitare più tipi di contenitori o liquidi senza la necessità di cambiare parti. Alcuni produttori dispongono di macchinari in grado di gestire più formati di bottiglia attraverso l'uso di un unico pezzo di attrezzatura purché la viscosità dei liquidi sia costante. Anche i macchinari dovrebbero essere facili da aggiornare, il che è particolarmente importante man mano che il business cresce.
Valore chiave delle soluzioni di automazione della viscosità nella linea di confezionamento
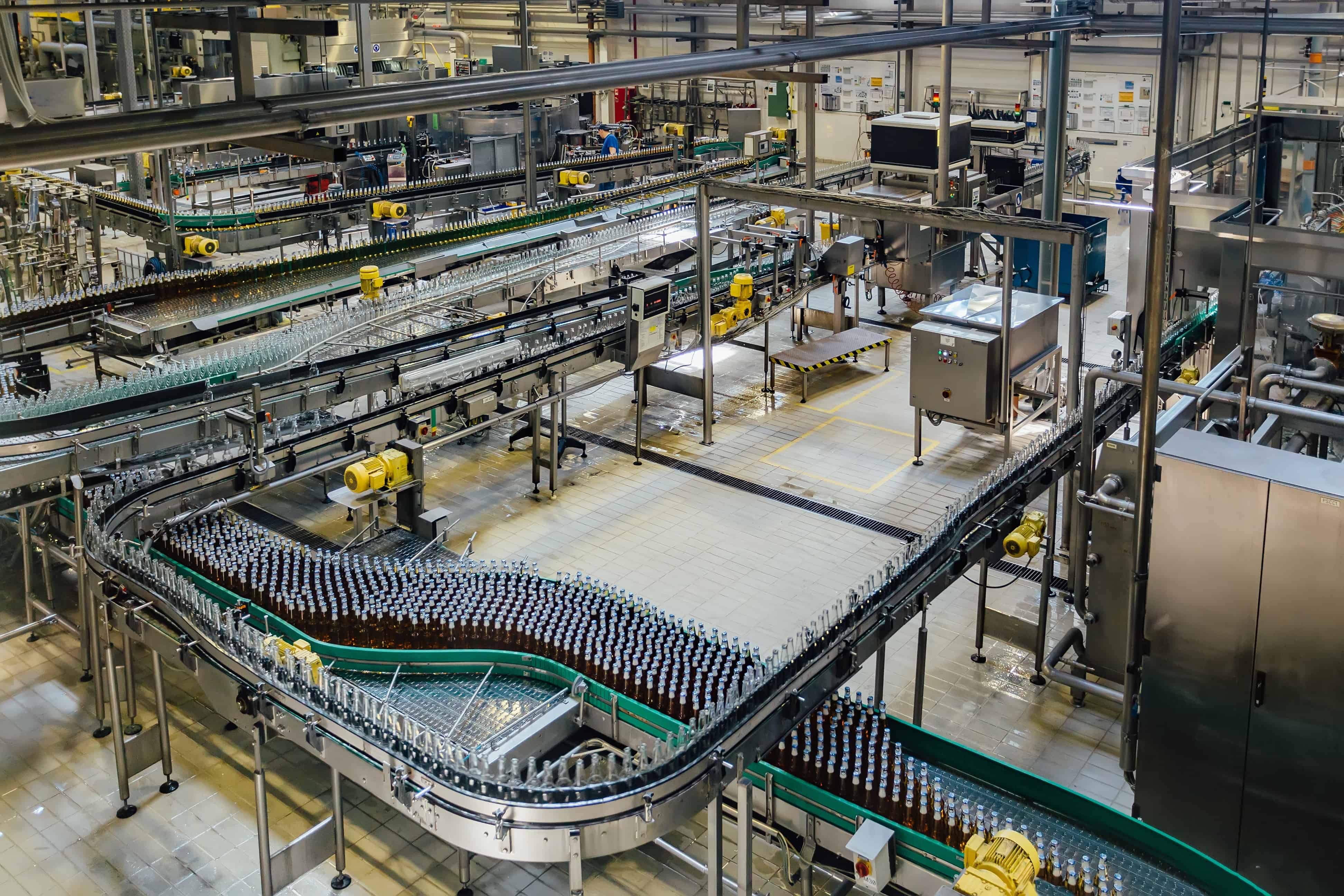
I fattori ampi e significativi che rendono la gestione della viscosità importante praticamente in ogni applicazione di riempimento:
- Qualità: Misurazione della viscositàoring del prodotto liquido nelle fasi di lavorazione e trasporto che precedono l'operazione di riempimento può garantire che prima del riempimento la qualità/consistenza del prodotto sia adeguata.
- Ripetibilità tra lotti: Per garantire la coerenza da lotto a lotto e per mantenere un livello / peso costante, il controllo della viscosità è essenziale.
- Riduzione dei rifiuti e riduzione dei costi: Accurate operazioni di riempimento significano che la quantità esatta di prodotto viene consegnata durante l'imballaggio, risparmiando tonnellate di materiali extra che potrebbero essere potenzialmente utilizzati in altro modo altrimenti. Significa anche riduzione degli scarti e degli scarti, anche nelle normative più severe, minimizzando così i costi.
- Efficienza: Monitoraggio senza problemi e in tempo realeoring della viscosità può far risparmiare molto tempo e fatica coinvolti nell'analisi offline del campione e nel prendere decisioni sul processo basate su tale analisi.
- Ambiente: L'automazione della viscosità può ottimizzare i processi CIP / SIP. Ridurre la quantità di utilizzo di liquidi / materiali per la pulizia fa bene all'ambiente.
- Fabbrica intelligente - vantaggi della digitalizzazione e dell'automazione: I dati di processo acquisiti dai sensori possono essere utilizzati in molti altri modi: pianificazione della manutenzione della macchina, diagnosi QC, analisi delle cause alla radice, scambio di informazioni tra strutture per decisioni decentralizzate e molto altro. La capacità di caricare diversi lavori / modelli per diversi fluidi utilizzando le informazioni sulla viscosità si trasforma in vantaggi di fondamentale importanza, consentendo alle aziende di trarre vantaggio dall'Industria 4.0 e dalle tecnologie di automazione. Diventano più adattabili alle mutevoli esigenze dei consumatori. Ulteriori informazioni utilizzando il collegamento sottostante.
Elaborazione alimentare digitale: driver per i produttori che abbracciano l'Industria 4.0
Le fluttuazioni di temperatura, le condizioni dell'attrezzatura di miscelazione, il tipo e le condizioni dei substrati, le formulazioni della pastella, le interazioni delle fasi di processo ei parametri del tempo di miscelazione possono alterare la qualità e le prestazioni del prodotto nei lotti di miscelazione e rivestimento della pastella. Nei settori a margine sottile come i prodotti da forno, gli alimenti ricoperti di pastella e i dolciumi, il ...
Misurazione della viscosità e sfide di processo
Gli ingegneri e gli operatori degli impianti nelle linee di confezionamento si rendono conto della necessità di effettuare misurazioni della viscosità e di intervenire attraverso appropriate azioni correttive per ottenere una scorrevolezza di alta qualità, costante e prevedibile del prodotto liquido / semiliquido. Tuttavia, effettuare queste misurazioni li ha messi alla prova nel corso degli anni.
I campioni prelevati offline sono semplicemente inaffidabili e non adatti per le operazioni di confezionamento di liquidi
Monitoring la viscosità di un fluido in un processo spesso significa prelevare un campione del fluido da un serbatoio o da una tubazione e portare il campione in un laboratorio dove il suo flusso e le proprietà reologiche vengono misurati su un viscosimetro o reometro da laboratorio. Sulla base dei risultati, l'operatore del processo deve essere informato se il fluido ha la viscosità desiderata o, se sono necessarie ulteriori azioni, devono essere effettuate nuove misurazioni dopo l'intervento. Questo sistema è chiamato controllo offline o manuale, con diversi ovvi svantaggi: richiede molto tempo e spesso è impreciso anche con operatori esperti. Molto spesso i risultati arrivano troppo tardi per salvare un batch.
L'alternativa è usare un viscosimetro in linea che monitorerà continuamente la viscosità del fluido di processo durante tutto il processo. Questo strumento fornisce un segnale in uscita che, se visualizzato, fornisce all'operatore le informazioni necessarie per controllare il processo. In alternativa, le uscite del viscosimetro sono collegate a un PLC (controllore logico programmabile) / DCS (sistema di controllo digitale) per il controllo automatico del processo.
Problemi con viscosimetri convenzionali per l'installazione in linea
I viscosimetri di processo tradizionali incontrano problemi legati al flusso del fluido nelle installazioni di miscelazione di tubazioni e serbatoi. In generale, questi viscosimetri di vecchia generazione non funzionano correttamente in un flusso turbolento. Gli strumenti rotanti funzioneranno solo fino a una certa portata massima. Il flusso deve essere controllato per viscosimetri a caduta di pressione. I problemi relativi al flusso per questi tipi vengono evitati installando il viscosimetro sulla linea di by-pass e condizionando il flusso del campione per adattarlo allo strumento. Il tempo di risposta dello strumento è quindi correlato alle condizioni di flusso, poiché è necessaria una velocità di rinnovo del campione adeguata per un controllo efficace. Inoltre, gli strumenti utilizzati in un ambiente di processo devono essere robusti e in grado di resistere a qualsiasi materiale corrosivo che possono incontrare, specialmente durante la pulizia.
Rheonics' Soluzioni per migliorare l'efficienza e l'agilità della linea di confezionamento
La misurazione e il controllo automatizzati della viscosità in linea sono fondamentali per monitorare/controllare la viscosità durante le operazioni di riempimento e garantire che i parametri della macchina della linea di confezionamento siano regolati in base alla viscosità del prodotto. Rheonics offre le seguenti soluzioni per il controllo del processo e l'ottimizzazione dell'efficienza nella linea di confezionamento.
Misuratori di viscosità e densità
- In linea Viscosità misure: Rheonics' SRV è un dispositivo di misurazione della viscosità in linea ad ampia gamma in grado di fornire misurazioni della viscosità (insieme a misurazioni della temperatura) e rilevare i cambiamenti di viscosità all'interno di qualsiasi flusso di processo in tempo reale.
- In linea Viscosità e densità misure: Rheonics' SRD è uno strumento di misurazione simultanea della densità e della viscosità in linea (insieme alle misurazioni della temperatura). Se la misurazione della densità è importante per le vostre operazioni, SRD può soddisfare le vostre esigenze, con capacità operative simili a SRV insieme a misurazioni accurate della densità.
Questi strumenti danno un segnale di uscita e lettura su un pannello software che, se visualizzato, fornisce all'operatore le informazioni necessarie per controllare il processo. In alternativa, può essere possibile inviare l'uscita a un controllore di processo automatico. I sistemi di controllo integrati consentono di utilizzare efficacemente le informazioni sulla viscosità / densità nella linea di processo.
Integrato, chiavi in mano qualità gestione per operazioni di linea di riempimento
Rheonics offre una soluzione integrata chiavi in mano per la gestione della qualità composta da:
- In linea Viscosità misure: Rheonics'SRV - un dispositivo di misurazione della viscosità in linea ad ampia gamma con misurazione della temperatura del fluido incorporata
- Rheonics Process Monitor: un avanzato controller di tracciamento predittivo monitorare e controllare in tempo reale le variazioni delle condizioni di processo
- Rheonics Reopulse con automaticamente in Sistemi dOsing: Un sistema autonomo di Livello 4 che non scende a compromessi con i limiti di viscosità prefissati e attiva automaticamente valvole o pompe di by-pass per dosare in modo adattivo i componenti della miscela nelle fasi di lavorazione precedenti le operazioni di riempimento.
Rheonics Process Monitor
Il sensore SRV è posizionato in linea, quindi misura continuamente la viscosità (e la densità in caso di SRD). Gli avvisi possono essere configurati per notificare all'operatore l'azione necessaria oppure l'intero processo di gestione può essere completamente automatizzato con RPTC (Rheonics Controller di monitoraggio predittivo). L'utilizzo di un SRV nella linea di riempimento determina un miglioramento della produttività e dei margini di profitto e garantisce la conformità normativa. Rheonics i sensori hanno un fattore di forma compatto per una semplice installazione OEM, retrofit e un facile ampliamento su tutte le linee della fabbrica. Non richiedono manutenzione o riconfigurazioni. I sensori offrono risultati accurati e ripetibili indipendentemente da come o dove sono montati, senza necessità di camere speciali, guarnizioni in gomma o protezione meccanica. Non utilizzando materiali di consumo e non richiedendo ricalibrazione, SRV e SRD sono estremamente facili da utilizzare, con conseguenti costi di gestione estremamente bassi. In qualità di costruttore di macchine o integratore di sistemi di automazione, puoi saperne di più sulla facilità di integrazione rheonics sensore nella tua linea sulla nostra pagina dedicata ai System Integrator.
Una volta stabilito l’ambiente del processo, di solito è richiesto poco sforzo per mantenere l’integrità e la coerenza dei sistemi: gli operatori possono fare affidamento sullo stretto controllo con Rheonics soluzione di gestione della linea di confezionamento di liquidi.
I densimetri a sonda in linea hanno un vantaggio nel riempimento automatizzato basato sul peso
Per un riempimento automatico preciso (ad esempio, metodo volumetrico), può essere particolarmente importante monitorare e controllare la densità. La densità può fluttuare a causa di bolle d'aria nel liquido e variazioni di temperatura o ricetta.
I misuratori di portata Coriolis forniscono misurazioni del flusso di massa ma presentano alcuni svantaggi come:
- Procedure di calibrazione che richiedono tempo e installazione difficile
- Difficoltà nella pulizia: i misuratori di portata Coriolis sono difficili da pulire, soprattutto quando il fluido ha un notevole contenuto di solidi. Li rende inadatti a soddisfare gli standard igienici interni alle fabbriche.
- Tempi di riempimento più lunghi: con la tecnologia di pesatura o la misurazione della portata massica, sono necessari circa cinque secondi per riempire una bottiglia. La misurazione della portata subisce le maggiori fluttuazioni nella velocità di riempimento, con un tempo che varia tra due e cinque secondi.
D'altro canto, Rheonics Gli SRD sono progettati e realizzati per la più semplice integrazione in un ambiente di produzione continua. Non hanno camere speciali e possono essere facilmente rimosse per la pulizia o l'ispezione. Le sonde SRD sono sigillate ermeticamente per il Clean-in-place (CIP) e supportano il lavaggio ad alta pressione con connettori M69 IP12K. SRD è un prodotto unico che sostituisce tre diversi strumenti per le misurazioni di viscosità, densità e temperatura.
Linee di confezionamento può sfruttare al meglio i progressi della tecnologia di automazione Rheonics
Rheonics i sistemi di automazione includono funzionalità che vanno oltre i sistemi legacy come algoritmi avanzati di controllo dei processi integrati e monitoraggio statisticooring, monitoraggio del dispositivo intelligenteoring e monitoraggio dello stato degli assetoring. Forniscono i dati sui processi e sulle condizioni delle risorse sia alle operazioni che alla manutenzione, consentendo modi nuovi ed efficienti per integrare i processi di lavoro e migliorare la tempestività e l'accuratezza delle decisioni, aspetti fondamentali considerando la velocità e la portata delle operazioni all'interno di una linea di confezionamento di prodotti liquidi.
Rendere i sistemi CIP più intelligenti
Rheonics SRV (e SRD) non sono solo conformi CIP/SIP, ma monitorano anche la pulizia delle linee del fluido mediante monitoraggiooring la viscosità (e densità) del detergente/solvente durante la fase di pulizia. Eventuali piccoli residui vengono rilevati dal sensore, consentendo all'operatore di decidere quando la linea è pulita/adatta allo scopo. In alternativa, SRV (e SRD) fornisce informazioni al sistema di pulizia automatizzato per garantire una pulizia completa e ripetibile tra un ciclo e l'altro, garantendo così la piena conformità agli standard sanitari degli impianti di produzione alimentare/farmaceutica. Ulteriori informazioni su come rheonics i sistemi di viscosità ottimizzano i sistemi CIP per ridurre i tempi di pulizia/tempi di inattività. Ciò significa anche un notevole risparmio di liquidi/materiali per la pulizia. Scopri di più in che modo SRV è compatibile con CIP e, allo stesso tempo, aiuta a ottimizzare il processo CIP.
Rheonics'Vantaggio
Fattore di forma compatto, nessuna parte mobile e nessuna manutenzione
Rheonics' SRV e SRD hanno un fattore di forma molto piccolo per una semplice installazione OEM e retrofit. Consentono una facile integrazione in qualsiasi flusso di processo. Sono facili da pulire e non richiedono manutenzione o riconfigurazioni. Hanno un ingombro ridotto che consente l'installazione in linea in qualsiasi linea di processo, evitando qualsiasi spazio aggiuntivo o necessità di adattatori.
Design igienico e sanitario
Rheonics SRV e SRD sono disponibili in tri-clamp e connessioni DIN 11851 oltre a connessioni al processo personalizzate.
Sia SRV che SRD sono conformi ai requisiti di conformità al contatto alimentare secondo le normative FDA e UE degli Stati Uniti.
Elevata stabilità e insensibilità alle condizioni di montaggio: qualsiasi configurazione possibile
Rheonics SRV e SRD utilizzano un esclusivo risonatore coassiale brevettato, in cui due estremità dei sensori ruotano in direzioni opposte, annullando le coppie di reazione sul loro montaggio e quindi rendendoli completamente insensibili alle condizioni di montaggio e alle portate. L'elemento sensore si trova direttamente nel fluido, senza requisiti di alloggiamento speciale o gabbia protettiva.
Letture accurate istantanee sulla "fluidità" - Panoramica completa del sistema e controllo predittivo
Rheonics' Reopulse il software è potente, intuitivo e comodo da usare. Il fluido di processo in tempo reale può essere monitorato sull'IPC integrato o su un computer esterno. Più sensori distribuiti in tutto l'impianto sono gestiti da un unico dashboard. Nessun effetto della pulsazione di pressione del pompaggio sul funzionamento del sensore o sulla precisione della misurazione. Nessun effetto di vibrazione.
Misure in linea, non è necessaria alcuna linea di bypass
Installa direttamente il sensore nel tuo flusso di processo per eseguire misurazioni di viscosità (e densità) in tempo reale. Non è richiesta alcuna linea di bypass: il sensore può essere immerso in linea; la portata e le vibrazioni non influiscono sulla stabilità e l'accuratezza della misurazione.
Installazione semplice e nessuna riconfigurazione / ricalibrazione necessaria: zero manutenzione / tempi di fermo macchina
Nell'improbabile eventualità di un sensore danneggiato, sostituire i sensori senza sostituire o riprogrammare l'elettronica. Sostituzioni immediate sia per il sensore che per l'elettronica senza aggiornamenti del firmware o modifiche alla calibrazione. Montaggio facile. Disponibile con connessioni al processo standard e personalizzate come NPT, Tri-Clamp, DIN 11851, Flangia, Varinline e altri collegamenti sanitari e igienici. Nessuna camera speciale. Facilmente rimovibile per la pulizia o l'ispezione. SRV è disponibile anche con DIN11851 e tri-clamp connessione per un facile montaggio e smontaggio. Le sonde SRV sono sigillate ermeticamente per il Clean-in-place (CIP) e supportano il lavaggio ad alta pressione con connettori M69 IP12K.
Rheonics gli strumenti sono dotati di sonde in acciaio inossidabile e, opzionalmente, forniscono rivestimenti protettivi per situazioni speciali.
Basso consumo energetico
Alimentazione 24 V CC con assorbimento di corrente inferiore a 0.1 A durante il normale funzionamento.
Tempi di risposta rapidi e viscosità compensata in temperatura
L'elettronica ultraveloce e robusta, combinata con modelli computazionali completi, rendono Rheonics dispositivi tra i più veloci, versatili e accurati del settore. SRV e SRD forniscono misurazioni accurate della viscosità (e della densità per SRD) in tempo reale ogni secondo e non sono influenzati dalle variazioni della portata!
Ampie capacità operative
RheonicsGli strumenti sono costruiti per effettuare misurazioni nelle condizioni più difficili.
SRV è disponibile con la più ampia gamma operativa nel mercato del viscosimetro di processo in linea:
- Range di pressione fino a 5000 psi
- Intervallo di temperatura da -40 fino a 200 ° C
- Intervallo di viscosità: 0.5 cP fino a 50,000 cP (e superiore)
SRD: strumento singolo, tripla funzione - Viscosità, temperatura e densità
Rheonics' SRD è un prodotto unico che sostituisce tre diversi strumenti per le misurazioni di viscosità, densità e temperatura. Elimina la difficoltà di collocare tre diversi strumenti e fornisce misurazioni estremamente accurate e ripetibili nelle condizioni più difficili.
gestire erogazione / riempimento in modo più efficiente, ridurre i costi e migliorare la produttività
Integra un SRV nella linea di processo e assicurati la coerenza nel corso degli anni. SRV monitora e controlla costantemente la viscosità (e la densità in caso di SRD) e attiva le valvole in modo adattivo per il dosaggio dei componenti della miscela. Ottimizza il processo con un SRV e sperimenta meno arresti, minor consumo di energia, minori non conformità e risparmi sui costi dei materiali. E alla fine di tutto, contribuisce a una migliore redditività e a un ambiente migliore!
Clean in place (CIP) e Sterilizzazione in loco (SIP)
SRV (e SRD) monitora la pulizia delle linee del fluido tramite monitoring la viscosità (e densità) del detergente/solvente durante la fase di pulizia. Eventuali piccoli residui vengono rilevati dal sensore, consentendo all'operatore di decidere quando la linea è pulita/adatta allo scopo. In alternativa, SRV (e SRD) fornisce informazioni al sistema di pulizia automatizzato per garantire una pulizia completa e ripetibile tra un ciclo e l'altro, garantendo così la piena conformità agli standard sanitari degli impianti di produzione alimentare.
Cos'è il CIP? Ottimizzazione dei sistemi CIP (Clean In Place) con misurazioni di viscosità e densità in linea
Cos'è il CIP? Nei sistemi CIP, la pulizia avviene senza smontare il sistema. CIP si riferisce a tutti quei sistemi meccanici e chimici che sono necessari per preparare le attrezzature per la lavorazione degli alimenti, sia dopo un ciclo di lavorazione che ha prodotto normale ...
Design e tecnologia dei sensori superiori
L'elettronica sofisticata e brevettata è il cervello di questi sensori. SRV e SRD sono disponibili con connessioni al processo standard del settore come ¾" NPT, DIN 11851, flangia e Tri-clamp consentendo agli operatori di sostituire un sensore di temperatura esistente nella linea di processo con un SRV/SRD che fornisce informazioni sui fluidi di processo estremamente preziose e utilizzabili come la viscosità oltre a una misurazione accurata della temperatura utilizzando un Pt1000 integrato (disponibile DIN EN 60751 Classe AA, A, B) .
Elettronica costruita per soddisfare le tue esigenze
Disponibile sia nella custodia del trasmettitore che in un montaggio su guida DIN di dimensioni ridotte, l'elettronica del sensore consente una facile integrazione nelle linee di processo e all'interno degli armadi delle apparecchiature delle macchine.
Facile da integrare
Molteplici metodi di comunicazione analogica e digitale implementati nell'elettronica del sensore rendono il collegamento a PLC industriali e sistemi di controllo semplici e diretti.
Opzioni di comunicazione analogica e digitale
Opzioni di comunicazione digitale opzionali
Conformità ATEX e IECEx
Rheonics offre sensori a sicurezza intrinseca certificati ATEX e IECEx per l'uso in ambienti pericolosi. Questi sensori sono conformi ai requisiti essenziali di salute e sicurezza relativi alla progettazione e costruzione di apparecchiature e sistemi di protezione destinati all'uso in atmosfere potenzialmente esplosive.
Le certificazioni di sicurezza intrinseca e antideflagrante possedute da Rheonics consente inoltre la personalizzazione di un sensore esistente, consentendo ai nostri clienti di evitare i tempi e i costi associati all'identificazione e al test di un'alternativa. Possono essere forniti sensori personalizzati per applicazioni che richiedono da una unità fino a migliaia di unità; con tempi di consegna di settimane anziché di mesi.
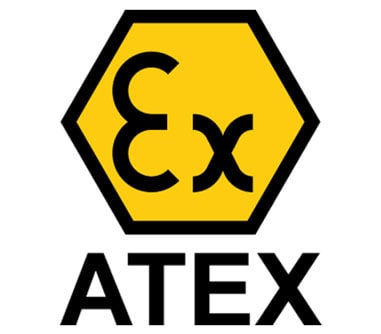
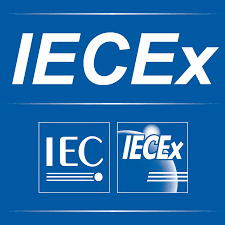
Implementazione
Installa direttamente il sensore nel flusso di processo per eseguire misurazioni di viscosità e densità in tempo reale. Non è necessaria alcuna linea di bypass: il sensore può essere immerso in linea; la portata e le vibrazioni non influenzano la stabilità e la precisione della misurazione. Ottimizza le prestazioni di miscelazione fornendo test ripetuti, consecutivi e coerenti sul fluido.
Luoghi di controllo qualità in linea
- In vasche
- Nei tubi di collegamento tra i vari contenitori di lavorazione
Strumenti / sensori
SRV Viscosimetro OR an SRD per una maggiore densità
Rheonics Selezione dello strumento
Rheonics progetta, produce e commercializza sistemi innovativi di rilevamento e monitoraggio dei fluidioring sistemi. Precisione costruita in Svizzera, RheonicsI viscosimetri e i densimetri in linea hanno la sensibilità richiesta dall'applicazione e l'affidabilità necessaria per sopravvivere in un ambiente operativo difficile. Risultati stabili – anche in condizioni di flusso avverse. Nessun effetto della caduta di pressione o della portata. È ugualmente adatto alle misurazioni di controllo qualità in laboratorio. Non è necessario modificare alcun componente o parametro per misurare l'intero intervallo.
Prodotto / i suggerito / i per l'applicazione
- Ampia gamma di viscosità: monitora l'intero processo
- Misurazioni ripetibili in fluidi newtoniani e non newtoniani, fluidi monofase e multifase
- Parti a contatto con il fluido ermetiche 316L in acciaio inossidabile
- Misurazione della temperatura del fluido integrata
- Fattore di forma compatto per una semplice installazione in linee di processo esistenti
- Facile da pulire, nessuna manutenzione o riconfigurazione necessaria
- Strumento unico per la misura della densità di processo, viscosità e temperatura
- Misurazioni ripetibili in fluidi sia newtoniani che non newtoniani, fluidi monofase e multifase
- Costruzione interamente in metallo (acciaio inossidabile 316L)
- Misurazione della temperatura del fluido integrata
- Fattore di forma compatto per una semplice installazione in tubi esistenti
- Facile da pulire, nessuna manutenzione o riconfigurazione necessaria