I modi chiave nelle misurazioni e nella gestione della viscosità e della densità svolgono un ruolo centrale nelle fasi di produzione dell'olio lubrificante sono i seguenti:
- Operazioni di miscelazione accurate e controllo qualità in linea
- Formulazione e sviluppo di nuovi lubrificanti
- Test integrato
Introduzione
L'odierno mercato dell'olio lubrificante impone requisiti di qualità del prodotto sempre più severi. Oltre all'industria automobilistica, chimica, edilizia, tessile, infrastrutture, agricoltura, estrazione mineraria e trivellazione petrolifera, edilizia, acciaio e cemento, energia eolica, nautica, industria aerospaziale e settori energetici per olio motore, olio idraulico, funi metalliche e cuscinetti, sono i aree di applicazione chiave in cui i lubrificanti sono ampiamente utilizzati. Nel settore edile, i lubrificanti sono principalmente utilizzati nelle macchine movimento terra per le loro caratteristiche antiusura, ottima capacità lubrificante e resistenza alla corrosione. I lubrificanti sono utilizzati anche come fluidi idraulici nell'industria siderurgica per varie apparecchiature tra cui altiforni, cuscinetti, carrucole, ascensori e motori, tra gli altri. Inoltre, i lubrificanti vengono utilizzati negli oli motore per impieghi gravosi, negli oli per assali e trasmissioni e nei grassi.
Le formulazioni sono sempre più numerose e complesse. Oltre ai requisiti di agilità di produzione, il Lube Oil Blending Plant (LOBP) deve far fronte alle pressioni sui margini di un mercato dei lubrificanti altamente competitivo. Molti clienti ora vogliono consegne su richiesta e tempi di consegna più brevi. Ciò significa che gli impianti di miscelazione dei lubrificanti potrebbero dover produrre lotti più piccoli. Raggiungere obiettivi di qualità può essere difficile, a causa di uno scarso controllo del processo, dell'errore umano, della contaminazione incrociata o della variabilità delle materie prime. La capacità di un impianto di miscelazione di lubrificanti di massimizzare la produttività delle risorse, ottenere miscele su specifica ogni volta e mantenere la flessibilità per rispondere alle mutevoli esigenze del mercato è di fondamentale importanza.
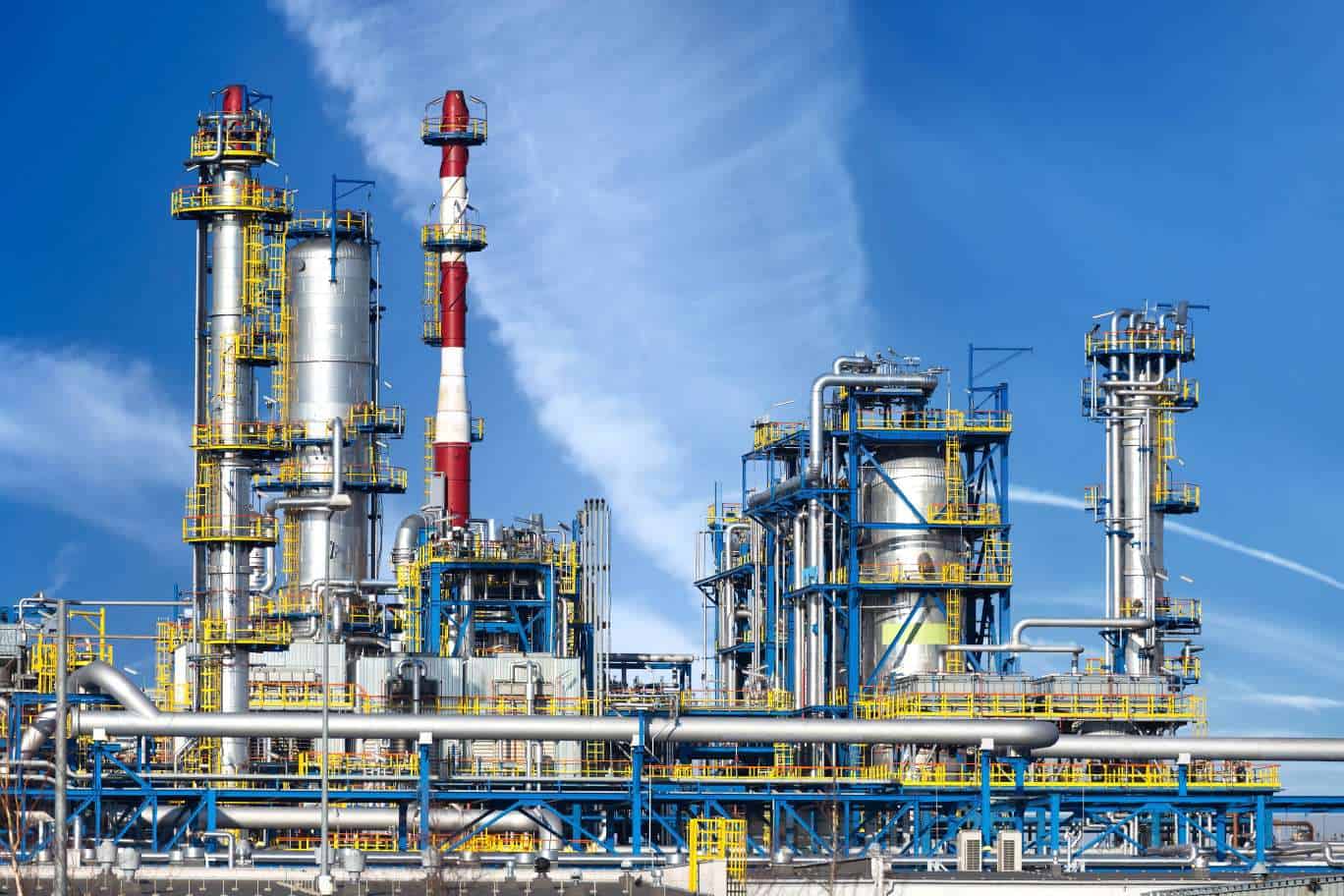
Che cos'è la miscelazione dell'olio lubrificante?
Il processo di produzione di lubrificanti finiti da oli base e additivi è invariabilmente descritto come miscelazione dell'olio piuttosto che come produzione di olio perché non ha luogo alcuna reazione chimica significativa e la miscelazione si basa principalmente su un'operazione di miscelazione. Tuttavia, il funzionamento economico di un moderno impianto di miscelazione è di fondamentale importanza per il processo complessivo di fornitura ai clienti dei lubrificanti corretti della qualità e delle prestazioni corrette. La miscelazione dei lubrificanti può essere relativamente facile; la gestione di un impianto di miscelazione non lo è certamente.
Approfondimenti di mercato e applicazioni industriali
Si prevede che la dimensione del mercato globale dei lubrificanti raggiungerà i 166 miliardi di dollari entro il 2025, secondo un nuovo rapporto di Grand View Research, Inc. Si prevede che si espanderà a un CAGR del 3.7% durante il periodo di previsione. Le vendite di automobili in rapida crescita, principalmente in paesi come India, Cina, Stati Uniti e Brasile, stanno guidando la crescita.
Segmentazione dei lubrificanti per applicazione e alcuni esempi:
- Lubrificanti per autoveicoli – Oli motore, oli per ingranaggi, fluidi per trasmissioni
- Lubrificanti industriali – Oli idraulici, oli per compressori, oli per ingranaggi
- Fluidi per la lavorazione dei metalli: fluidi da taglio, oli per elettroerosione, oli per presse e laminazione
- Grassi – Per cuscinetti a rulli, grassi per alte temperature, grassi per giunti di ingranaggi, grassi biodegradabili
- Lubrificanti marini – Oli motore per motori a pistoni, oli per sistemi, oli per cilindri
- Oli per motori industriali e privati – Per motori diesel, per motori a gas, per motori HFO (Heavy Fuel Oil)
Segmentazione per prodotti:
- Lubrificanti a base di olio minerale
- Lubrificanti sintetici
- Lubrificanti a base biologica
Applicazioni
Quali problemi si verificano se la viscosità di un lubrificante è troppo alta o troppo bassa?
Se un la viscosità del lubrificante è troppo alta, il lubrificante può avere problemi di scorrevolezza. Ciò può comportare:
- Più attrito e più calore, il che
- accelera il processo di ossidazione, accorciando la vita del lubrificante;
- favorisce la formazione di vernici e morchie; e
- aumenta il consumo di energia, poiché potrebbe essere necessaria più potenza per superare il calore eccessivo e mantenere il sistema in funzione in un intervallo di temperatura appropriato
- Maggiore usura, che può tradursi in maggiori tempi di fermo macchina per le riparazioni e una minore durata dei componenti
- Scarsa pompabilità con avviamento a freddo, aumento del rischio di danni alle apparecchiature o guasti all'avvio
- Scarsa antischiuma e scarsa demulsività (separabilità dall'acqua)
Se un la viscosità del lubrificante è troppo bassa, il fluido potrebbe non ricoprire e proteggere sufficientemente le parti come previsto. Le conseguenze possono includere:
- Usura eccessiva, che porta a più riparazioni/sostituzioni di componenti component
- Maggiore attrito e calore, favorendo un'ossidazione più rapida, una maggiore formazione di vernici e morchie e un maggiore consumo di energia
- Maggiore vulnerabilità a danni o guasti dei componenti, specialmente ad alte temperature, carichi elevati e basse velocità
- Maggiore suscettibilità all'impatto della contaminazione delle particelle
La misurazione della viscosità robusta e accurata in condizioni di processo difficili (replicata nei test) è essenziale per garantire la qualità del prodotto finale dei lubrificanti durante la produzione e il riempimento di oli lubrificanti. Solo una misurazione della viscosità ripetibile e accurata durante la produzione del prodotto garantisce una qualità costante del prodotto e consente di risparmiare tempo di produzione.
Dove le misurazioni della viscosità aggiungono valore alla catena?
Produzione di olio lubrificante: miscelazione
Vari additivi vengono miscelati nell'olio base per migliorarne le proprietà e formulare olio lubrificante. L'olio viene miscelato con additivi per conferirgli le proprietà fisiche desiderate (come la capacità di resistere alle basse temperature). La selezione degli additivi viene effettuata in base alle specifiche dell'olio lubrificante desiderate. Per produrre qualsiasi olio lubrificante, vengono utilizzate fondamentalmente 3 materie prime:
- Olio base
- Additivi
- Miglioratore dell'indice di viscosità (modificatore di viscosità)
A questo punto, l'olio lubrificante viene sottoposto a una serie di test di controllo qualità che ne valutano la viscosità.
La miscelazione dei lubrificanti può sembrare relativamente semplice. Tuttavia, ci sono due problemi principali che devono essere considerati:
- Evitando la necessità di mescolare nuovamente o correggere una miscela fuori specifica
- Ridurre al minimo la produzione di olio sporco
Le operazioni di miscelazione manuale nella produzione di lubrificanti pongono serie sfide nelle operazioni quotidiane quali: lunghi tempi di processo, bassa flessibilità nella gestione delle ricette e frequenti interventi dell'operatore. Queste sfide erano state direttamente collegate alla produttività, alla redditività e alla sicurezza delle operazioni presso l'impianto di lubrificazione.
Formulazione e sviluppo di un nuovo lubrificante industriale
La metodologia generale per lo sviluppo di un lubrificante industriale nuovo o migliorato è essenzialmente la stessa di quella per un olio motore automobilistico, con alcune differenze. È ancora costoso e richiede tempo. La scelta dell'olio base e degli additivi più adatti è di solito relativamente facile.
Una volta selezionata una formulazione iniziale “best-guess”, il primo passo è testarla in semplici test di laboratorio a basso costo. Un ampio numero di test di viscosità e densità diventa essenziale per valutare le proprietà fisiche o chimiche dei lubrificanti. I test per le proprietà fisiche includono viscosità a bassa temperatura, viscosità ad alta temperatura e densità (gravità specifica). La capacità degli ingegneri della formulazione di eseguire automaticamente questi prototipi di campioni miscelati durante l'intero ciclo di temperatura è fondamentale per valutare i punti di forza e di debolezza dei campioni.
Controllo di qualità
La maggior parte delle applicazioni degli oli lubrificanti richiede che siano non resinosi, di colore chiaro, inodori e resistenti all'ossidazione. Oltre una dozzina di test fisici e chimici vengono utilizzati per classificare e determinare il grado degli oli lubrificanti. I test fisici comuni includono misurazioni di viscosità, peso specifico e colore, mentre i test chimici tipici includono quelli per punti di infiammabilità e fuoco.
Probabilmente la singola proprietà più importante di un olio lubrificante è la sua viscosità. Un fattore nella formazione di film lubrificanti in condizioni sia di film spesso che di film sottile, la viscosità influenza la generazione di calore in cuscinetti, cilindri e ingranaggi. Determina inoltre la facilità con cui le macchine possono essere avviate a freddo e regola l'effetto di tenuta dell'olio e il tasso di consumo o perdita. Per qualsiasi attrezzatura, il primo elemento essenziale per risultati soddisfacenti è utilizzare un olio di viscosità adeguata per soddisfare le condizioni operative.
Sono necessari vari test di densità e viscosità per valutare le proprietà e le prestazioni sia degli oli base che degli additivi utilizzati come materie prime con cui miscelare i lubrificanti finiti. Poiché un impianto di miscelazione è un altro anello dell'intera catena di approvvigionamento, la capacità del personale dell'impianto di miscelazione di produrre lubrificanti finiti della qualità corretta dipende in parte dalla capacità dei fornitori di oli base e additivi di fornire materie prime di qualità adeguata.
- Per gli oli base, i metodi standard per la misurazione della viscosità cinematica sono ASTM D445 e IP 71
- La viscosità a bassa temperatura e a basso taglio è importante per prevedere la possibilità di "legatura dell'aria" negli oli motore dopo che i veicoli sono rimasti a basse temperature per un periodo considerevole. Si ritiene che il metodo Brookfield ASTM D5133 sia correlato a questi problemi e si consiglia di eseguire questo test su nuove formulazioni di olio. Tuttavia, richiede tempo e non consente facilmente prove su un gran numero di campioni, e quindi non è applicabile per l'uso in impianti di miscelazione di lubrificanti. Per gli oli di base, le proprietà di flusso a bassa temperatura sono una guida migliore per la loro idoneità all'uso in oli per motori automobilistici, fluidi per trasmissioni automatiche e alcuni oli per ingranaggi e oli idraulici.
Test integrato
I lubrificanti sono fluidi complessi e altamente ingegnerizzati che svolgono una varietà di lavori protettivi e funzionali: forniscono una pellicola idrodinamica tra i componenti in movimento, compresa l'erogazione di calore, la sospensione dei contaminanti, la neutralizzazione degli acidi e la prevenzione della corrosione e così via. L'olio lubrificante nei motori IC è esposto a varie sollecitazioni a seconda della qualità del carburante, delle condizioni ambientali e dei parametri operativi che ne modificano le proprietà fisiche e chimiche fino a degradarsi. Per evitare un guasto al motore, l'olio deve essere cambiato prima che perda le sue proprietà protettive. Allo stesso tempo, un cambio d'olio non necessario è indesiderato per motivi ambientali ed economici. Per programmare in modo ottimale l'intervallo di cambio dell'olio, è necessario monitorare le condizioni fisiche e chimiche effettive dell'olio. La condizione dell'olio motore fornisce informazioni sullo stato effettivo del motore e quindi supporta il rilevamento precoce di possibili guasti del motore.
La viscosità è considerata uno dei parametri più importanti per le proprietà lubrificanti dell'olio e la sua inclusione nel monitoraggio onlineoring sistemi sono stati raccomandati da diversi studi. Comunemente il deterioramento chimico dell'olio (dovuto ad esempio all'ossidazione) è associato ad un aumento della viscosità, mentre l'usura meccanica (“cracking” delle molecole della catena organica) e la diluizione del carburante portano ad una diminuzione della viscosità. Pertanto, la conoscenza della viscosità in tempo reale offre vantaggi significativi per misurare l'invecchiamento dell'olio, l'ingresso di contaminanti durante le operazioni commerciali e prevenire incipienti guasti meccanici dovuti alla perdita delle proprietà di lubrificazione dell'olio.
Sfide con il monitoraggio dei processi tradizionalioring e tecniche di controllo qualità
Miscelazione e controllo qualità
Il campionamento è una tecnica comune e convenzionale di QC e monitoring il processo di miscelazione. Il successo del campionamento dipende in larga misura dal tipo di bottiglie campione e dai metodi di campionamento: quantità, accuratezza, affidabilità e utilità dei dati che possono essere acquisiti dal campione. È necessario prelevare campioni di oli base e additivi prima della miscelazione, potrebbe essere necessario prelevare campioni di miscele durante la miscelazione e campioni di prodotti finiti dopo la miscelazione. È necessario prelevare un campione rappresentativo di ciascun lotto di lubrificante miscelato, a fini di controllo del processo, controllo di qualità e garanzia della qualità. È molto importante che i campioni vengano prelevati mentre l'apparecchiatura è in funzione (sia di miscelazione che di pompaggio), in modo che il campione sia rappresentativo del processo in corso. Questo metodo richiede molto lavoro e tempo ed è soggetto a errori e imprecisioni.
Test integrato
Nella pratica comune, l'olio motore viene cambiato a un tempo o intervallo di chilometraggio costante secondo le raccomandazioni dei produttori di olio lubrificante o OEM. Questo metodo di cambio dell'olio non si basa sulla reale condizione dell'olio del motore specifico e può essere sostituito prima del raggiungimento della fine della sua vita utile o dopo il superamento della sua vita utile. Questo è antieconomico, in quanto sarà uno spreco e deteriorerà anche il motore.
In alcuni lubrificanti monitoring tecniche, tali intervalli flessibili di scarico dell'olio sono determinati mediante monitoraggio continuooring parametri caratteristici del motore e di guida (quali, ad esempio, distanza percorsa, velocità e temperatura dell'olio). Il corretto intervallo di cambio dell'olio viene quindi stimato dai corrispondenti algoritmi che elaborano questi parametri. Questi algoritmi sono sviluppati empiricamente mediante estesi studi sul campo. Gli algoritmi utilizzano sostanzialmente tali parametri per stimare lo stato dell'olio in modo indiretto. Queste tecniche non monitorano direttamente le proprietà fisiche del lubrificante, pertanto problemi critici come la contaminazione del carburante possono essere trascurati. Un'eccessiva contaminazione del lubrificante può portare a cambiamenti drammatici nelle proprietà del lubrificante, impedendo al lubrificante di svolgere le sue funzioni richieste. Tuttavia, idealmente, la valutazione delle condizioni dell'olio dovrebbe basarsi esclusivamente su parametri misurati direttamente nell'olio stesso.
I viscosimetri meccanici ed elettromeccanici convenzionali progettati principalmente per misurazioni di laboratorio sono difficili da integrare nel controllo e nel monitoraggiooring ambiente. L'attuale metodologia di test nei laboratori fuori sede non è ottimale ed è costosa a causa delle sfide logistiche della spedizione e degli elevati costi fissi. Nell'industria dei lubrificanti, il viscosimetro universale standard Saybolt è lo strumento standard per determinare la viscosità dei lubrificanti tra 70 e 210 gradi Fahrenheit (21 e 99 gradi Celsius). La viscosità viene misurata nel Saybolt Universal second, che è il tempo in secondi richiesto affinché 50 ml di olio vengano svuotati da una tazza del viscosimetro Saybolt attraverso un orifizio del tubo calibrato a una determinata temperatura. Questo metodo dipende fortemente dall'esperienza dell'operatore, è soggetto a errori e rende la produzione JIT sempre più difficile.
Perché la misurazione della viscosità in tempo reale per la miscela di oli lubrificanti è monitorataoring & Controllo di qualità importante?
Esistono numerosi vantaggi motivazionali dal punto di vista dei costi, dell'ambiente e della logistica per le misurazioni della viscosità online in tempo reale per il monitoraggio delle miscele di lubrificantioring & controllo di qualità. L'automazione della viscosità nel lubrificante migliora la flessibilità e le prestazioni del processo per soddisfare i requisiti just-in-time.
I vantaggi principali sono i seguenti:
- Evita la ricombinazione per migliorare la produttività dell'impianto e per evitare ritardi: Dover rimescolarsi dovrebbe essere evitato ove possibile. Ricombinare significa utilizzare energia aggiuntiva (un costo significativo) e una potenziale riduzione della capacità annua dell'impianto di miscelazione. Reblending può anche significare mantenere un cliente in attesa della consegna di un prodotto chiave. I sistemi di miscelazione automatizzati con gestione della viscosità in linea consentono un controllo di qualità efficace delle materie prime, eliminano la necessità di rimescolamento e ottimizzano la qualità dell'olio di lubrificazione finale.
- Riduzione degli interventi manuali e dei costi operativi: In un impianto di miscelazione di lubrificanti, le spese operative sono fortemente generate a causa del coinvolgimento manuale (supervisione e funzionamento) richiesto nei processi di routine. Il tempo impiegato per completare una miscela ha un effetto significativo sull'efficienza e sull'economicità di un impianto di miscelazione. La sostituzione dei dispositivi di misurazione della viscosità convenzionali con viscosimetri robusti rende il controllo di qualità più semplice e affidabile.
- Mantieni il controllo del processo di miscelazione e ottieni un tempo di miscelazione ottimale per la migliore qualità del prodotto e il massimo risparmio sui costi: Se una miscela viene miscelata troppo velocemente, potrebbe non essere completamente omogenea (e quindi fuori specifica) e il tempo di miscelazione dovrà essere allungato. Se si impiega troppo tempo a miscelare una miscela, sarà stata sprecata energia (sia nella miscelazione che nel riscaldamento) e l'attrezzatura di miscelazione non sarà disponibile per la miscela successiva. Misurazioni della viscosità in linea durante il processo di miscelazione del lubrificante
- Vantaggi logistici: L'analisi della viscosità del lubrificante in linea ridurrebbe il numero di campioni inviati ai laboratori fuori sede e i relativi costi. I risultati delle condizioni continue delle analisi in loco ridurrebbero anche i costi/la manodopera di spedizione e l'errore di campionamento.
- Tempi di risposta più rapidi: L'analisi della viscosità in situ ridurrebbe/eliminerebbe il ritardo tra il campionamento e la ricezione di una risposta dal laboratorio.
- Informazione accurata: Il vero valore dell'andamento dei dati in tempo reale è che fornisce una finestra sul sistema di mixaggio. Nei test integrati, monitoraggio della viscosità in tempo realeoring Le tecniche quantificano i cambiamenti nelle proprietà fisiche del lubrificante e forniscono una lettura più accurata delle condizioni dell'olio, riducendo così il consumo di olio e fornendo i mezzi per diagnosticare i guasti dei componenti.
- Ambiente: L'utilizzo del petrolio può essere massimizzato tramite il monitoraggio onlineoring sistemi, con conseguente riduzione degli sprechi, a vantaggio dell’ambiente.
Rheonics' Soluzioni per il controllo e la garanzia della qualità dei processi di raffineria
La misurazione automatizzata e in tempo reale della viscosità in linea è fondamentale per il monitoraggio delle condizioni dell'oliooring. Rheonics offre le seguenti soluzioni, basate su un risonatore torsionale bilanciato, per il controllo e l'ottimizzazione del processo in tempo reale e il monitoraggio delle condizioni dell'olio motoreoring:
- In linea Viscosità misure: Rheonics'SRV è un dispositivo di misurazione della viscosità in linea ad ampio raggio con misurazione della temperatura del fluido integrata ed è in grado di rilevare in tempo reale le variazioni di viscosità all'interno di qualsiasi flusso di processo.
- In linea Viscosità e densità misure: Rheonics'SRD è uno strumento di misurazione simultanea in linea di densità e viscosità con misurazione della temperatura del fluido integrata. Se la misurazione della densità è importante per le tue operazioni, SRD è il sensore migliore per soddisfare le tue esigenze, con capacità operative simili all'SRV e misurazioni accurate della densità.
I processi di miscelazione continua richiedono che il materiale “su specifica” venga realizzato il più rapidamente possibile. RheonicsLa soluzione di miscelazione in linea garantisce un prodotto costantemente conforme alle specifiche con un utilizzo ottimale dell'attrezzatura e un'interazione minima con l'operatore. Ciò consente di lavorare alle velocità massime con regolazioni automatiche e di ridurre i tempi di miscelazione senza sacrificare la qualità.
La misurazione automatizzata della viscosità in linea tramite SRV o SRD elimina le variazioni nelle tecniche di prelievo dei campioni e di laboratorio utilizzate per la misurazione della viscosità con i metodi tradizionali. Il sensore è posizionato in linea in modo da misurare continuamente la viscosità del lubrificante (e la densità in caso di SRD). Entrambi i sensori hanno un fattore di forma compatto per una semplice installazione OEM e retrofit. Non richiedono manutenzione o riconfigurazioni. Entrambi i sensori offrono risultati accurati e ripetibili indipendentemente da come o dove sono montati, senza bisogno di camere speciali, guarnizioni in gomma o protezione meccanica. Non utilizzando materiali di consumo, SRV e SRD sono estremamente facili da usare.
Caratteristiche principali di SRV e SRD:
- I controlli elettronici basati su menu sono potenti e facili da usare.
- Monitoraggio della temperatura integratooring utilizzando un RTD PT1000 ad alta precisione.
- Segnali di uscita multipli: visualizza la temperatura e viscosità compensata in temperatura
- Controllo automatico della viscosità: i sensori sono preimpostati ma
- La registrazione dei dati – la data e il codice temporale vengono registrati automaticamente, creando un audit trail e semplificando la misurazione delle prestazioni e dell'andamento della qualità.
- Sicurezza e avvisi – progettato per impedire modifiche non autorizzate e attivare un allarme quando vengono raggiunti i setpoint in modo che gli operatori possano agire rapidamente.
- Impostazioni di memoria a modifica rapida – per le linee di processo che utilizzano più di un fluido, questa funzione semplifica la modifica delle impostazioni.
Supportare gli ingegneri della formulazione nei laboratori
Anche se il sensore SRV è costruito per garantire un controllo di qualità completo del lubrificante miscelato durante la produzione. Lo stesso sensore viene utilizzato anche in laboratorio per la ricerca sulla formulazione. Rheonics I moduli termici autonomi vengono utilizzati dagli ingegneri della formulazione per testare rapidamente nuovi campioni nell'intero intervallo di funzionamento termico. STCM è costruito per funzionare specificamente con SRV e SRD. L'apparecchiatura ha le stesse dimensioni di una piccola macchina da caffè da tavolo e dispone di riscaldamento e raffreddamento a stato solido per raggiungere l'intera gamma operativa.
Il principio alla base può essere utilizzato come un sistema di campionamento e test automatizzato basato su carosello. Un vantaggio chiave dell'utilizzo dell'SRV per la ricerca sulla formulazione è che lo stesso sensore viene quindi installato sul controllo delle materie prime in entrata, sugli impianti pilota e sulle linee di produzione finali, in modo che non vi siano discrepanze nel sistema di misurazione utilizzato nell'intero ecosistema di lubrificazione.
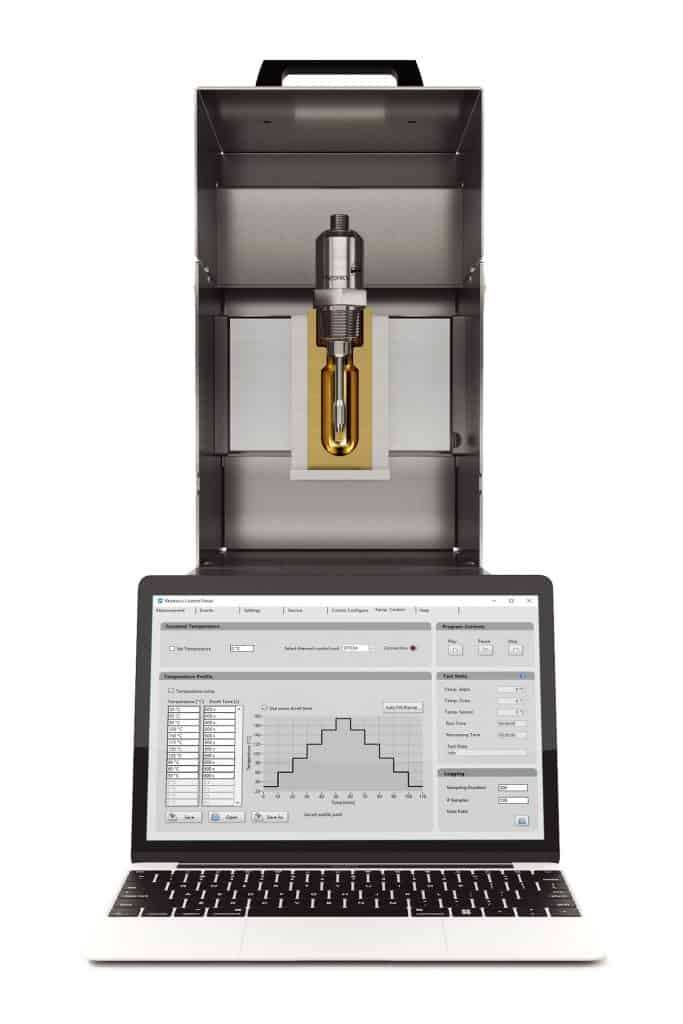
Rheonics'Vantaggio
Fattore di forma compatto, nessuna parte mobile e nessuna manutenzione
Rheonics' SRV e SRD hanno un fattore di forma molto piccolo per una semplice installazione OEM e retrofit. Consentono una facile integrazione in qualsiasi flusso di processo. Sono facili da pulire e non richiedono manutenzione o riconfigurazioni. Hanno un ingombro ridotto che consente l'installazione in linea in qualsiasi linea di processo, evitando qualsiasi spazio aggiuntivo o necessità di adattatori.
Elevata stabilità e insensibilità alle condizioni di montaggio: qualsiasi configurazione possibile
Rheonics SRV e SRD utilizzano un esclusivo risonatore coassiale brevettato, in cui due estremità dei sensori ruotano in direzioni opposte, annullando le coppie di reazione sul loro montaggio e quindi rendendoli completamente insensibili alle condizioni di montaggio e alle portate. L'elemento sensore si trova direttamente nel fluido, senza requisiti di alloggiamento speciale o gabbia protettiva.
Letture accurate istantanee sulla qualità della produzione - Panoramica completa del sistema e controllo predittivo
Rheonics' Reopulse il software è potente, intuitivo e comodo da usare. Il fluido di processo in tempo reale può essere monitorato sull'IPC integrato o su un computer esterno. Più sensori distribuiti in tutto l'impianto sono gestiti da un unico dashboard. Nessun effetto della pulsazione di pressione del pompaggio sul funzionamento del sensore o sulla precisione della misurazione. Nessun effetto di vibrazione.
Misure in linea, non è necessaria alcuna linea di bypass
Installa direttamente il sensore nel tuo flusso di processo per eseguire misurazioni di viscosità (e densità) in tempo reale. Non è richiesta alcuna linea di bypass: il sensore può essere immerso in linea; la portata e le vibrazioni non influiscono sulla stabilità e l'accuratezza della misurazione.
Installazione semplice e nessuna riconfigurazione / ricalibrazione necessaria: zero manutenzione / tempi di fermo macchina
Nell'improbabile eventualità di un sensore danneggiato, sostituire i sensori senza sostituire o riprogrammare l'elettronica. Sostituzioni immediate sia per il sensore che per l'elettronica senza aggiornamenti del firmware o modifiche alla calibrazione. Montaggio facile. Disponibile con connessioni al processo standard e personalizzate come NPT, Tri-Clamp, DIN 11851, Flangia, Varinline e altri collegamenti sanitari e igienici. Nessuna camera speciale. Facilmente rimovibile per la pulizia o l'ispezione. SRV è disponibile anche con DIN11851 e tri-clamp connessione per un facile montaggio e smontaggio. Le sonde SRV sono sigillate ermeticamente per il Clean-in-place (CIP) e supportano il lavaggio ad alta pressione con connettori M69 IP12K.
Rheonics gli strumenti sono dotati di sonde in acciaio inossidabile e, opzionalmente, forniscono rivestimenti protettivi per situazioni speciali.
Basso consumo energetico
Alimentazione 24 V CC con assorbimento di corrente inferiore a 0.1 A durante il normale funzionamento.
Tempi di risposta rapidi e viscosità compensata in temperatura
L'elettronica ultraveloce e robusta, combinata con modelli computazionali completi, rendono Rheonics dispositivi tra i più veloci, versatili e accurati del settore. SRV e SRD forniscono misurazioni accurate della viscosità (e della densità per SRD) in tempo reale ogni secondo e non sono influenzati dalle variazioni della portata!
Ampie capacità operative
RheonicsGli strumenti sono costruiti per effettuare misurazioni nelle condizioni più difficili.
- Range di pressione fino a 5000 psi
- Intervallo di temperatura da -40 fino a 200 ° C
SRV ha la gamma operativa più ampia sul mercato per il viscosimetro di processo in linea:
- Intervallo di viscosità: 0.5 cP fino a 50,000 cP
RSD: Strumento singolo, tripla funzione – Viscosità, Temperatura e Densità
Rheonics' SRD è un prodotto unico che sostituisce tre diversi strumenti per le misurazioni di viscosità, densità e temperatura. Elimina la difficoltà di collocare tre diversi strumenti e fornisce misurazioni estremamente accurate e ripetibili nelle condizioni più difficili.
- Intervallo di viscosità: 0.5 cP fino a 3,000 cP
- Gamma di densità: da 0 a 4 g/cc (da 0 a 4000 kg/m3)
Ottenere informazioni accurate sulla qualità del lubrificante attraverso misurazioni dirette, ridurre i costi e migliorare la produttività
Integrare un SRV/SRD nella linea di processo per programmare in modo ottimale gli intervalli di cambio del lubrificante e ottenere significativi risparmi sui costi. Rispetto all'approccio indiretto dell'utilizzo di algoritmi per prevedere lo stato reale, le misurazioni della viscosità del lubrificante fornirebbero un'immagine fisica reale della lubrificazione consentendo il rilevamento di possibili guasti ai cuscinetti/motore in avvicinamento o stati anomali. E alla fine di tutto, contribuisce a una migliore linea di fondo e un ambiente migliore!
Clean in place (CIP)
SRV (e SRD) sono sensori autopulenti: l'utilizzo del fluido in linea per pulire il sensore mentre esegue le misurazioni riduce la manutenzione non programmata. Eventuali piccoli residui vengono rilevati dal sensore, consentendo all'operatore di decidere quando la linea è pulita per lo scopo. In alternativa, questi sensori forniscono informazioni al sistema di pulizia automatizzato per garantire una pulizia completa e ripetibile tra i cicli di produzione.
Design e tecnologia dei sensori superiori
L'elettronica sofisticata e brevettata di terza generazione guida questi sensori e valuta la loro risposta. SRV e SRD sono disponibili con connessioni al processo standard del settore come ¾" NPT e 3" Tri-clamp consentendo agli operatori di sostituire un sensore di temperatura esistente nella linea di processo con un SRV/SRD che fornisce informazioni sui fluidi di processo estremamente preziose e utilizzabili come la viscosità oltre a una misurazione accurata della temperatura utilizzando un Pt1000 integrato (disponibile DIN EN 60751 Classe AA, A, B) .
Elettronica costruita per soddisfare le tue esigenze
Disponibile sia in un alloggiamento del trasmettitore che in un montaggio su guida DIN con fattore di forma ridotto, l'elettronica del sensore consente una facile integrazione nelle tubazioni di processo e all'interno degli armadi delle apparecchiature delle macchine.
gestire mescolanza in modo più efficiente, ridurre i costi e migliorare la produttività
Integra un SRV nella linea di processo e assicurati la coerenza nel corso degli anni. SRV monitora e controlla costantemente la viscosità (e la densità in caso di SRD) e attiva le valvole in modo adattivo per il dosaggio dei componenti della miscela. Ottimizza il processo con un SRV e sperimenta meno arresti, minor consumo di energia, minori non conformità e risparmi sui costi dei materiali. E alla fine di tutto, contribuisce a una migliore redditività e a un ambiente migliore!
Design e tecnologia dei sensori superiori
L'elettronica sofisticata e brevettata è il cervello di questi sensori. SRV e SRD sono disponibili con connessioni al processo standard del settore come ¾" NPT, DIN 11851, flangia e Tri-clamp consentendo agli operatori di sostituire un sensore di temperatura esistente nella linea di processo con un SRV/SRD che fornisce informazioni sui fluidi di processo estremamente preziose e utilizzabili come la viscosità oltre a una misurazione accurata della temperatura utilizzando un Pt1000 integrato (disponibile DIN EN 60751 Classe AA, A, B) .
Elettronica costruita per soddisfare le tue esigenze
Disponibile sia nella custodia del trasmettitore che in un montaggio su guida DIN di dimensioni ridotte, l'elettronica del sensore consente una facile integrazione nelle linee di processo e all'interno degli armadi delle apparecchiature delle macchine.
Facile da integrare
Molteplici metodi di comunicazione analogica e digitale implementati nell'elettronica del sensore rendono il collegamento a PLC industriali e sistemi di controllo semplici e diretti.
Opzioni di comunicazione analogica e digitale
Opzioni di comunicazione digitale opzionali
Conformità ATEX e IECEx
Rheonics offre sensori a sicurezza intrinseca certificati ATEX e IECEx per l'uso in ambienti pericolosi. Questi sensori sono conformi ai requisiti essenziali di salute e sicurezza relativi alla progettazione e costruzione di apparecchiature e sistemi di protezione destinati all'uso in atmosfere potenzialmente esplosive.
Le certificazioni di sicurezza intrinseca e antideflagrante possedute da Rheonics consente inoltre la personalizzazione di un sensore esistente, consentendo ai nostri clienti di evitare i tempi e i costi associati all'identificazione e al test di un'alternativa. Possono essere forniti sensori personalizzati per applicazioni che richiedono da una unità fino a migliaia di unità; con tempi di consegna di settimane anziché di mesi.
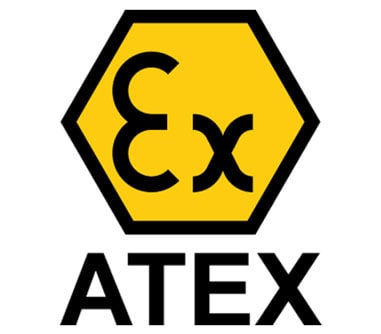
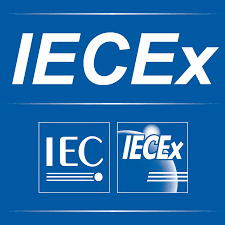
Implementazione
Installa direttamente il sensore nel flusso di processo per eseguire misurazioni di viscosità e densità in tempo reale. Non è necessaria alcuna linea di bypass: il sensore può essere immerso in linea; la portata e le vibrazioni non influenzano la stabilità e la precisione della misurazione. Ottimizza le prestazioni di miscelazione fornendo test ripetuti, consecutivi e coerenti sul fluido.
Luoghi di controllo qualità in linea
- In vasche
- Nei tubi di collegamento tra i vari contenitori di lavorazione
Strumenti / sensori
SRV Viscosimetro OR an SRD per una maggiore densità
Rheonics Selezione dello strumento
Rheonics progetta, produce e commercializza sistemi innovativi di rilevamento e monitoraggio dei fluidioring sistemi. Precisione costruita in Svizzera, RheonicsI viscosimetri e i densimetri in linea hanno la sensibilità richiesta dall'applicazione e l'affidabilità necessaria per sopravvivere in un ambiente operativo difficile. Risultati stabili – anche in condizioni di flusso avverse. Nessun effetto della caduta di pressione o della portata. È ugualmente adatto alle misurazioni di controllo qualità in laboratorio. Non è necessario modificare alcun componente o parametro per misurare l'intero intervallo.
Prodotto / i suggerito / i per l'applicazione
- Ampia gamma di viscosità: monitora l'intero processo
- Misurazioni ripetibili in fluidi newtoniani e non newtoniani, fluidi monofase e multifase
- Parti a contatto con il fluido ermetiche 316L in acciaio inossidabile
- Misurazione della temperatura del fluido integrata
- Fattore di forma compatto per una semplice installazione in linee di processo esistenti
- Facile da pulire, nessuna manutenzione o riconfigurazione necessaria
- Strumento unico per la misura della densità di processo, viscosità e temperatura
- Misurazioni ripetibili in fluidi sia newtoniani che non newtoniani, fluidi monofase e multifase
- Costruzione interamente in metallo (acciaio inossidabile 316L)
- Misurazione della temperatura del fluido integrata
- Fattore di forma compatto per una semplice installazione in tubi esistenti
- Facile da pulire, nessuna manutenzione o riconfigurazione necessaria